About : standard furniture owner
Title : standard furniture owner
standard furniture owner
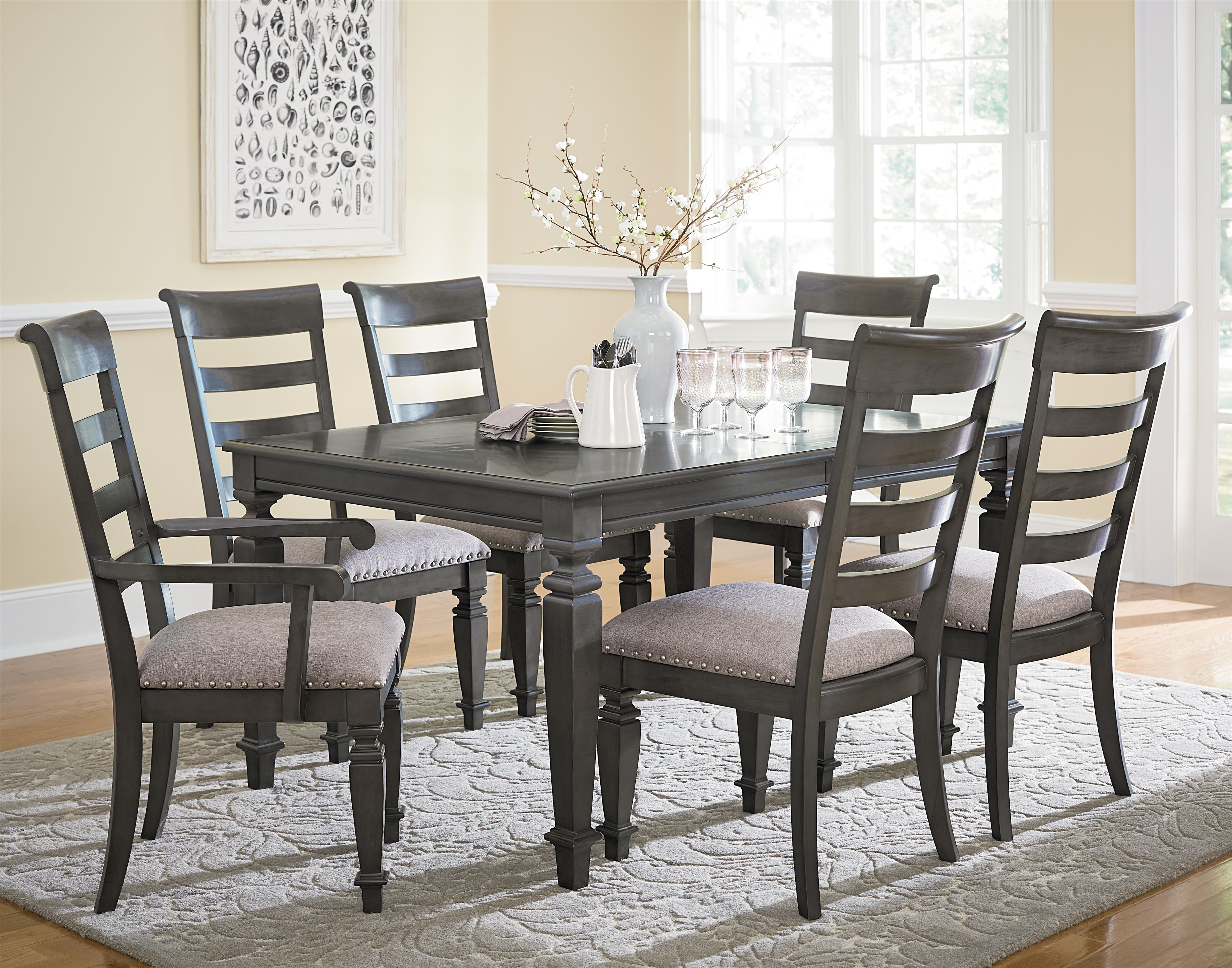
this video is brought to you by sailrite.visit sailrite.com for all your project supplies, tools and instructions.this video tutorial will show the steps required to make your own enclosure aft curtain. everydetail from patterning, sewing, and installing zippers and fasteners will be shown. makingyour own enclosure curtains may save you thousands compared to having a canvas shop to do it.it’s not as difficult as it looks, especially after watching this video. purchase all thesupplies needed to make enclosure curtains at sailrite. our aft curtain will be attached to the radararch of this maxum 2900 powerboat via awning track and rope. the awning rope will havea zipper sewn to it so it can easily be installed
and removed. sailrite carries many types ofawning track, but since this radar arch has a rather abrupt curve we will use flex-a-railawning track for this application. let’s get started and show you how to installthe awning track. the first step is to take measurements ofthe area the flex-a-rail awning track will need to extend. since the flex-a-rail is shippedin a few different lengths from sailrite we need to think about how many sticks we needand where each junction will fall. for this boat the center of the radar archto the coaming measures 95â€. the awning track comes in 44 or 90 inch lengths we willuse 2 each of 90†sections and 1 each of 44†section and butt them together.brian is going to mark a conservative 21â€
from center on both the port and starboardside of the radar arch. these marks will serve as a reference for creating a pattern so wecan bend the track appropriately. to make on the fiberglass he is using a pencil. he then measures up from the coaming to thespot where the track will begin to take a curve and places a mark. measure up on theopposite side and place a mark at that measurement also on that side.for easy reference when making the pattern he uses a strip of 3m filament strapping tapealong the marks and extends it to the top of the radar arch so it can be easily seen.it will also extend to the side of the radar arch here.to gain access for patterning he will unsnap
the bimini top from the radar arch. a sidenote: if you would like to see how we made the bimini top for this boat you will finda streaming video on our sailrite website showing that entire process.use some cardboard as a pattern being sure it covers the entire radius of the cornerand temporarily tape it in place along the curve. mark the locations where the strappingtape falls at the top and side and then trace the curve onto the cardboard pattern.repeat these steps for the starboard side. be sure to label the pattern for easy reference.sailrite’s flex-a-rail track is, as the name implies, flexible. but the curve we needis rather abrupt and does requires some special steps to achieve.this portion of the video will demonstrate
what is required.using the measurement we took on the boat (from coaming to beginning of cure transition)mark the track up from the end that amount, plus an extra inch for a fudge factor.starting at the mark on the pattern walk the track along the cardboard pattern to the pointwhere the curve transitions to an almost straight away and mark the track there also.“the two marks that i made here, i made one mark here that’s the beginning of mycrown then i made a markup here which is essentially the end of my crown. notice the end of mytrack isn’t going to be until up here but i do what to make a mark up here because ionly want to heat this section up. there is a just real gentle curve up here, we willbe able to do that on the boat. but were going
to heat up this sections and just bend thatsection.†using a heat gun on high heat brian will focusthe heat on the section he outlined. moving the heat gun over the track rotating the trackas he heats it up. the track will eventually start to take a bend. it will almost becomethe consistency of a spaghetti noodle that has cooked just long enough to start to takea bend. we have placed a timer on the video showing the approximate time length requiredbefore it can start to be bent. were going to skip ahead here from about 28seconds to 1 minute and 47 seconds. brian feels and tries to bend the track, butit is not quite ready, so he reheats it again. after about a half minute or so he tries again.after about 2 minutes 30 seconds it is starting
to bend slightly. after about 3 minutes hethinks it is just about ready to take the full bend. before bending insert the awningrope to help stabilize the opening and keep it from collapsing. do this quickly beforethe track cools again and become ridged. notice that he uses the cardboard patternas a reference so he can hand bend the track to replicate the curve on the pattern.the track has cooled to the point where it will no longer bend easily and he is not yethappy with the amount of bend. so he will remove the awning rope and reheat it oncemore. only as smaller sections needs bent more, so it will take less time since it isa smaller section of track that needs our attention.before bending again, insert the awning rope.
we are using keder awning rope here.does it match the pattern perfectly, no but it is close enough. notice that we can makemodifications by simply flexing it, so we can match it up to the curve on the radararch when we are inserting each screw. remove the keder or as some pronounce kederawning rope and inspect the tracks opening, if a wall has collapsed slightly you can openit back up by reheating that section and using a blunt object that fits almost perfectlybetween the walls of the track. our track’s walls are in good condition, but we want todemonstrate what should be done just in case yours is not. we are slightly heating up thetrack here, not enough to make modifications but we are still going to show you.so, if the tracks walls were hot enough this
cut off screw driver would be forcing thewall apart as they cool down and become ridged again.and that’s all it takes to force flex-a-rail awning track to take a sharp turn. comingup next we will show how to install this track to the boat’s radar arch.since the track will extend all the way to the coaming and the ends need to be cut tomatch the profile angle we need to tape it in place so we can mark it appropriately.remember we added an extra inch for the curve so we have some here we can cut off withoutlosing too much. we can mark the cut with a pencil trying to match it up with the coamingsurface. flex-a-rail track cuts easily with a hacksaw.some of you may be saying, “if the track
goes all the way to the coaming on both sidesof the boat how in the world is the awning rope going to be inserted in the track?â€good question! brian is determining which side of the track needs to have a cut outmade too and he will grind off one side of the wall (usually a 2†opening is enoughto allow the awing rope to be inserted). here he is using a grinder, but i prefer usinga dremel tool with a sanding drum. we like to predrill holes in our track beforetaking it to the boat for installation. this first hole will be very close to the end ofthe track. this hole will be almost directly over the coaming, so we will angle it backat about 45 degrees so we can drive the screw in at a slight angle avoiding the coamingobstacle. all our other holes will be driven
straight down. we like to position screwsholes about 4 to 6 inches apart. when we get to the curved section or crown we will switchour hole positions to about 4 to 5 inches apart there.since our main goal of using the awning track is to help prevent water from leaking pastthe aft curtain panel we want to also prevent the water from leaking at the base of theflex-a-rail awing track. to accomplish a total water tight seal we will use trimmable butyltape from sailrite. sure you could use a marine silicone, but that captures dirt and alsois a major pain to clean up off the fiberglass when it expands past the track. butyl tapealways stays flexible and is easy to remove from surfaces.if you don’t use it along the entire length
of the track it should be used as a beddingcompound for the screw holes. the holes that will be drilled in the fiberglass need tobe protected from possible leaking using the butyl tape around each drilled hole will bea perfect bedding sealant for the hole we make in the fiberglass.brian is now positioning the track and will temporally tape it in place. after ensuringthat it is where he wants it to lay he will drill a hole through the predrilled hole inthe track and into the fiberglass. we are using a 1/8 inch drill bit which is the perfectsize for the special screws that the flex-a-rail track uses.these stainless steel screws feature a flat head that fits perfectly in the opening ofthe track to allow passage of the awning rope.
a square head screwdriver also needs to beused. as each screw is inserted and tightened downyou will notice the butyl tape expands beneath the track. we recommend drilling and screwingone screw at a time. after the track is secured cleaning up theexcessive butyl tape that has been squeezed out is easily done by running a knife gentlybeside the track then rolling the butyl down creating a “snowball†like wad.here at the top we have to bend the track to match the radar arch, since it is a gradualcurve this is easily done. the butyl tape will actually help to hold the track in placeprior to drilling. butyl tape will act differently depending on the working temperatures. weare working in a temperature of about 65 degrees.
normal room temperature or cooler is optimalfor the consistency of the butyl tape when applying it to your job. after applied itworks in all temperatures. we did not show it, but we have installedthe port and starboard side tracks. now all we have left is the center section that willjoin them together. brian will make it to size, cut it, and then install it in the samemanner as what we have shown. always ensure that a screw is about one inch away from anyend where a junction is made between two tracks. the openings at the bottom of our track areless than 2 inches, we need to open them up more to make it easier to insert the awningrope in a future step. here you can see brian inserting the kederor keder awning rope into the track. coming
up next we mark where the zippers need tobe installed and also show you how to make a gorgeous zipper plaque to cover the zipperand protect it from the sun. our boat had old curtains which we are attachingand will use as a means to mark for where the new curtains will fall. we will need tomake two aft side curtains and a large aft curtain with a door. the old aft curtainswere attached via snaps to the radar arch. we will use the awning track and rope withzippers sewn to the awning rope to attach the new curtains.here brian is making on the fiberglass with a pencil where the door opening was located.we have a separate side curtain that attaches to a larger aft curtain. the zipper whichattaches the two is not directly over the
hard break (or corner). we will duplicatethe location where it rests at now, mainly because snaps are already installed to accommodatethe panels at the lower edge. however, if possible, it is always best to position thehard break (facings with zipper) as close to the corner as possible. why? the clearvinyl window material typically does not lay neatly at the hard turn, while the canvasand zipper do. next install the awning rope in the track.since our track has a rather sharp curve brian will have to pull it thru. when the rope reachesthe other side, pull it back out a few inches and cut it so it is exactly the entire lengthof the track. then push it back into the track so the ends are flush.then mark the awning rope with a pencil at
each location where a zipper needs to be installed.this is the door and these are the sides of the aft curtain which attach to the side curtains.i will state this one more time, for a better looking curtain try to positon the zipperwhich attaches the two closer to the hard turn at the corner.pull the awning rope out of the track and let’s get ready to install the zipper alongwith an awesome looking canvas plaque. here we are using a clear acrylic ruler tomeasure out some sunbrella marine grade fabric to size for our zipper cover. we are cuttinga strip of fabric that is 4 inches wide. and we used a soapstone pencil and here were usingthe sailrite edge hot knife to cut it out and keep the edges from unraveling. to saveon fabric we cut along the width of the fabric,
meaning we made a lot of 4 inch strips tocover the entire length of our awning rope. those need to be joined together. to do thiswe will sew a straight stitch along the edge about a half inch away from the raw edge.after that stitch is completed the fabric will be turned so the right side is facingup and a top stitch will be placed about 1/8 inch away from the seam’s fold. this iscalled a semi-flat-felled seam. be sure to sew through the bottom ⽠inch fold whilesewing this stitch. here is what the bottom side looks like andhere is the top side. all of our strips have been joined together to form one long lengththat is equal or slightly longer than our awning rope length.fold that assembly in half so the outside
surface is facing out (seam should be on theinside). then using a swing away 1†straight angle binder from sailrite and 1†bias bindingsew a binding over the two raw edges. brian checks the underside to be sure he likesthe stitch quality and where it is placed on the binding.this binder attachment folds the prefabricated 1 inch binding over the edge and keeps thestitch in the right spot. all brian has to do is fold the assembly evenly and push itup inside the edge of the binder’s feeder, the binder does all the rest of the work.he now creases the edge up against the shape edge of a table (do this only on a work table,as the abrasion may damage the table’s edge). i would recommend doing this prior to installingthe binding for an easier sewing job.
onto the keder or keder awning rope and applythe 3/8†wide seamstick for canvas (double sided tape) to the flange on the awning rope.baste the awning rope to the assembly we just made being sure to leave at least a half inchof extra canvas at the end. notice that the canvas is sticking out above the awning rope’stop edge, this is a preference and not a rule. what brian is trying to achieve is a slighttail that will cover the awning tracks edge slightly, as seen here.next we will sew this awning rope to the assembly so the stitch is right up against the rope’sedge. to accomplish this we are using a roping zipper foot left on this ultrafeed ls-1 sewingmachine. if you do not have this foot just sew as close as possible to the rope.as with any and most sewing applications do
some reversing at the beginning and end ofyou sewing. we will need to install three zippers to thisawning rope assembly. each of the three zippers will secure one curtain panel. we have applieda â¼â€ seamstick for canvas to the flange of the zipper on the correct side of the zipper.it is best to install the side of the zipper with the starter post or sometimes calledstarter pin on the awning rope. why? we believe it is easier to zipper each curtain in placewhen the zipper’s starter box is on the actual curtain then the box can be pushedonto the zipper’s pin and the slider pulled more easily.notice that we leave about 1 to 2 inches of space between zippers.to sew the zipper to the awning rope brian
places the deluxe 5 â½â€ magnetic guide downon the sewing machine. however, that is not typically needed when sewing zippers becausethe walking foot or presser foot often just rides up against the zipper’ teeth as itis sewn down. at the very end of this awning rope the lastof our three zippers is a little long. so the end will need to be cut off (this is theend with a factory stop) and a new stop will need to be made. we will use a cut sectionof 1†binding to accomplish that. it will be folded over the teeth and then sewn down.here is the outside surface and here is the inside surface. the opposite end was cut tothe correct length for our project and at that location the zippers had to be cut also,so we will need to install a zipper stop there
too. but before we do that lets finish thecanvas ends with binding. cut them so they are no less than â½â€ from the end of thezipper. then sew on a length of binding reversingat the beginning and end. this gives it a finished look. then use a hotknife to sealthe ends of the binding to keep them from unraveling. the awning rope now has zippersinstalled to the flange and it also has a protective fabric cover that adds a touchof class. coming up next we will be showing how to patternone of the sides for the aft curtains. our curtains could be secured to the radararch using snap instead of the awning track and rope. if snaps were used instead of theawing rope we will pattern the edge of our
panels about a half inch or inch outside therow of snaps on the radar arch. however, we are using awning rope and zippers so it mustbe fabricated before patterning can be done. here at the bottom edge we are securing 3mfilament strapping tape about a half inch (not more than an inch) away from the rowof snap studs on the boat. along the radar arch we are securing the strapping tape alongthe closest solid surface next to the awning rope/track. why? because it is much easierto pattern on a solid surface then one that is on a zipper and hidden by a canvas edge.once we are happy with the pattern we will transfer the pattern to the zipper’s flange.that will be coming up after we show how to set up the pattern. here 3/8†seamstickfor canvas is being applied over the strapping
tape. this provides a double sided tape tostick the pattern to for proper patterning. the strapping tape give us the ability toeasily remove the double sided tape after we are done.we are using dura skrim pattern material and we want it to be extra-large when we initiallypattern, but as we baste it in place we want to trim it to size for easier tensioning andfitting. always try to leave enough along each edge so it can be grabbed and fine-tunedeasily. here you can see brian making adjustmentsuntil everything is as nice and wrinkle free as it can be. do not pull so much on the duraskrim pattern material that you stretch it out of shape. continue to pattern and if neededcut to size until you are happy. we will show
this in double-time. next we will transfer the pattern’s topedge (along the awning rope edge) to the zipper’s flange on the awning rope. brian is happywith the way it looks, so he will trim along the top edge right along the side of the awningtrack’s edge. we could try to mark where the zipper falls on the pattern material asit is up now, but we always have better success basing the pattern to the zipper directly.only cut where the curtain will attach to the awning rope, leave the bottom intact.apply 3/8 inch basting tape for canvas along the flange edge of the zippers, on the correctside, the side that will face in towards the cabin. the zipper now needs to be zipped ontothe side that is sewn to the awning rope.
the pattern is still attached along the bottomedge and may not need to be adjusted along those edges. since the pattern is still injust about the right position, because it was pre-fitted along the solid surface toour radar arch, we can easily reattach it to the zipper’s flange.it is always a good idea to check that everything looks good before drawing on the pattern.brian is going to start by marking where the edge or corner of the curtain falls on thepattern material (this is between zippers). then he draws a line about 3 inches down indicatingwhere the middle of the zipper’s teeth are located.at the bottom edge he marks where the zipper stops.moving to the outside he marks around the
outer edge about ⾠inch away from the snapstuds on the boat. this will be the edge of the curtain.be sure to label the pattern for easy identification so you don’t get confused later on.instead of pulling the pattern material off the double sided tape along the zipper’sedge, instead unzip the zipper leaving it attached to the pattern material. we can thentake it to our table or floor and trace over the zipper more accurately. simply removethe pattern from the double sided tape everywhere else.at the work table strike a straight line along the inside edge where the larger aft curtainwill be zipped together with this side curtain. since the zipper was left basted to the patternmaterial we can trace up against the zipper’s
teeth ensuring a perfect line following theshape of the zipper on the pattern. the zipper can now be removed and the bastingtape on the zipper removed. this line we struck down against the zipper should be moved backa half inch. why? the zippers teeth will extend past this edge slightly because they willbe protected from the canvas strip we sewed to the awning rope in an earlier step.brian is not going to cut out the pattern, he instead likes to place the pattern underthe clear vinyl window material and trace on top of the lines.i think this is a good idea for the most part because the pattern material will not movearound as it is being traced and all markings on the pattern material weather inside oroutside the pattern will not accidently be
removed if it were cut out.here you can see this line being struck down a half inch away from the first line, as wediscussed earlier. all other lines will be traced directly on top of them. we like tomake the clear vinyl window material with a yellow grease pencil, as we are doing here,or a sharpie marker. clear vinyl window material should be cutwith scissors. it is now time to make the facings for thecurtain. for the underside facing we will use a vinyl fabric called shelter-rite, youcould just use the sunbrella or whatever fabric you have used for the outside surface as thefacing for the underside as well. to install the facings to the edges we couldjust make it for the outside surface only,
but that would make the inside look kind ofugly, as you would see hems and double sided tape through the clear vinyl.in general these are common finished width sizes of the facing strips along each edge.feel free to modify the finished widths as desired for your project.for the inside surface we will use a vinyl fabric called shelter-rite. as with any curtainpanel you have some choices regarding the facing material you want to use and whetheror not to use any on the inside surface, as discussed.you will notice that we have placed the clear vinyl onto of a soft cotton fabric to helpprotect the clear vinyl from abrasion while we work on the project.if your curtain panels have curved edges,
like this side, making your own facings asshown is a good idea. however, if your curtains are mostly straight edges you could just usethe prefabricated 2†facing that sailrite sells. why are we not using it for this project?well prefabricated facing is a production shortcut, but it does not take a curve well,it tends to wrinkle or not lay flat if the curve is rather abrupt. so, we are makingour own facings for this project. the shelter-rite has a shiny side and a dullside, we like the dull side to face up or out. so we are tracing on the shiny side withthe clear vinyl window facing outside surface up. the yellow grease pencil works best tomark shelter-rite fabric. as brian makes the facing for each side noticethe helpful jig that was made out of an old
ruler that was notched with a dremel toolat certain measurements, so the pencil could rest in the grooves to create facing stripsthe correct size. when using this jig be sure to hold it always perpendicular to the firststuck down line. now that the inside facing strips are cutout we can turn our attention to the outside facing strips. ours are sunbrella marine gradefabric. we will use the inside facing strips to make these. however, they need to be abouta â½ inch wider so a single hem can be created along the inside edge to give it a finishedlook. we used a soapstone pencil to mark on thissunbrella fabric and now we will cut them out with scissors. a hot knife could be usedto help prevent the edges from unraveling,
but since the edge will have a binding installedon it and the inside edge will be hemmed under those edges will not be visible and thus ahot knife cut edge is not necessary. as discussed earlier when adding the ⽠inchto one of the long sides be sure to hold the jig perpendicular to that edge. after the facing strips are cut to the correctshape and size it is time to sew them onto the curtain. we need to be sure to installthem on the correct inside or outside surface of the clear vinyl window material. alwaysstart with the inside facing strips, if you have them, and baste them in placing usingseamstick for canvas 3/8†on both long side. because the facing strips were patterned rightoff the edges of the clear vinyl, they should
fit almost perfectly. by placing the clear vinyl on top of a softcotton fabric we can rotate and move the clear vinyl around without possibly causing scratchesin our window materail. trim away any edge or end that may hang off.next up we will work on installing the sunbrella facing which will go on the outside surfaceof the curtain. this time apply the double sided seamstick for canvas 3/8†to the outerand inner edge of the curtain, as shown in the video.to apply the facing we will remove the basting tape’s transfer paper only from the rowof seamstick closest to the outside edge of the curtain. then carefully baste that edgedown. brian likes to baste all the outside
facing strips down then sew around the outsideperimeter of the curtain. because a hem along the inside edge is required he trims awaya portion of the end of each facing strip that is covered under the other to allow fora hem in a later step. in our previous enclosure curtain videos angelawould baste, sew and create a hem on one side at a time before proceeding to the next side’sfacing strip. as with any canvas project each creator has his or her preferences and youshould do it the way you like. i prefer angela’s method better than brian’s.now that brian has all the sides basted down along the outer edge only, he will now sewthe outer edge to hold them in place. keep this stitch very close to the edge asit will be covered by 1†bias binding in
a future step and we want to cover this stitchcompletely, so keep it about an 1/8†away from the edge. at the corner he will burythe needle in the fabric, lift the presser foot, roll the fabric around, lower the presserfoot and continues to sew. notice also that the soft cotton fabric isstill under the clear vinyl window material to protect it from accidental scratches thatmay occur while we are sewing. now we can create our single hem along theinside edge. peel of the transfer paper from the seamstick along this edge and just matchup the fold of this hem with the edge of the facing below for a great looking curtain.because brian sewed all the outside edges of the facing all at once he will have torip up a few stitches at each corner in order
to create the hem on this facing strip.the facing takes a rather abrupt curve here, so a few relief notches will need to be madeto allow the hem to lay flat. do not cut deeper than the hem allowance, which is a half inchhere. now the inside hem can be sewn down. sew aboutan 1/8 inch away from the folded edge. reversing to lock the stitch in place is really notneeded because the binding will cover the ends, but brian does it anyway because itis a good habit. please excuse the noise in the background.it is our 50 foot plotter bed plotting sail kits. the noise is the vacuum which holdsthe sailcloth down as the plotter cuts and marks each sail panel.here at the corner he will do some reversing,
remove the fabric, and start sewing from thenext hem on the opposite run of facing. continue doing this until all sides are sewnsecurely. to sewn on the binding we like to take theroll of binding and place it on a table with an awl or center post so it can spin as itis being used up. to sew the 1†sunbrella acrylic bias bindingin place around all the edges we will use the 1†swing away straight angle binderfrom sailrite. i do not recommend doing this job with a binder attachment device! yourjob, keep the assembly feeding consistently inside the opening of the binder attachment.let the binder do the job of keeping the stitch straight and the folding of the binding, youkeep your eye on the assembly being sure it
is pushed up into the opening so it catchesthe edge consistently for the stitch. the binding cannot easily take a 90 degreeturn so at any corners cut off the overrun binding, if any, and overlay the next runso it covers the previous and do some reversing at that corner to lock the stitch in place. this is a rather thick assembly consideringthat it is 30 gauge o’sea clear vinyl, sunbrella, shelter-rite and now a binding folded in half.so, as you feed this thick assembly into the opening of the binder you may have to helppush it through, since it is a rather a tight fit. after we are done using a hot knife to sealthe ends of the binding is a good idea.
next we will install the zippers. to do thisplace the pattern material over the curtain and mark the correct locations for the startand stops of each zipper. the nice thing about the soapstone pencil is the fact that it caneasily be erased if a mark is place at the wrong spot. brian is first installing the zipper whichwill zip to the awing rope. he will cut off the factory stop and remove the plastic slider.why? the boat owner wants to use metal sliders instead. apply to the flange of the zipper â¼â€ seamstickfor canvas. then we will baste the zipper to the curtain being sure the starter boxis beginning at the correct position we just
marked on the curtain. the zipper is attached to the inside surfaceof the curtain. since this zipper is used along the radar arch and the awning rope itwill be zipped to has a protective cover, we can leave the zipper’s teeth slightlyexposed making pulling the sider much easier. a zipper stop will be made with a strip of1†binding. you may want to opt for the ykk stainless steel top stops instead of thisbinding top. the zipper is too long so it will be cut sothe binding stop will start at the mark on the curtain indicating where the zipper shouldstop. since the slider was removed be sure to reinstall it before the stop is secured.
to sew on the zipper do some reversing tolock the stitch in place at the beginning then sew over the stitch that secured thebinding in place. why do i like using ykk stainless steel topstops instead of binding as a zipper stop? well, i can cut my zipper to size then removethe sider. sew on my zipper without having to worry about running in the slider whilesewing. then once the zipper is sewed on i can reinstall my slider and then crimp onmy ykk ss top stop. here we have to stop right before the slider and push it out of the waythen continue to sew. not a big deal, but it is a little more labor intensive. a typical question we get here at sailriteis, “can i sew this on my home machine?â€
well, for many canvas and upholstery jobsthat answer is often yes (depending on the job). however, enclosure curtains like thisdo require a heavy duty sewing machine. here at the corner we are going through 10 layersof fabric including the 30 gauge clear vinyl material. now that’s impressive. the ultrafeedis the world’s best portable industrial sewing machine, get yours today! brian is going to explain how he prefers toinstall zippers, here is brian… ok, so this is going to be our aft side paneland so typically you’ll put this panel on first. ah, when you go to hang your secondpanel on it, if you try to hold the panel with one hand and hold the zipper with theother hand it will be a lot easier if we put
not our starter box on this panel, but ratherour starter pin. that way when this zipper is stationary and in place you can have theother panel in your hand with the zipper slider and the starter box and you’ll be able todrop it onto that pin that is stationary and then with one hand basically zip it in place.right now i am having to hold the pin obviously since it is not sewn to anything. but whenit’s on place on the panel that will be a solid object it will be much easier to startit on there and zip it down. so basically the starter pin should be on the first panelup or the stationary object if possible. thanks brian! going back to the curtain andusing the pattern mark where the start and stop position for the zipper that will jointhe larger aft curtain to this smaller side
aft curtain. this zipper should be almostburied under the edge. why? this zipper runs vertically to join another panel and we wantto try to hide it from the elements to prolong its life. be sure not to burying it too deepas it is more difficult to slide the slider up and down, if so. the process for installation is just as itwas for the first zipper, except that this stitch which secures the zipper will not beon top of the stitch that holds the binding. it will be sewn with the zipper facing up,so it can be viewed while sewing. zipper the curtain onto the awning rope. thenget ready to install the fasteners along the bottom edge, that’s coming up next. to installsnaps along the bottom edge we will show two
snap installation tool systems; the snapritesystem and the pres-n-snap tool. to aid in snap positioning we will use thequick fit pin socket. this socket is reusable and simply snaps over an existing snap stud.then the fabric is pushed through the pin. i like to use about 5 quick fit pin socketsat a time then if my project requires more install the snaps first and then reuse theqfps again for the next set of 5 snaps. nice thing about the qfps system is that you canreposition a snap just be removing the pin and repositioning it in another location withouthaving to put a large hole in the project. ok, let’s start by showing installing asnaprite button with â¼â€ barrel and a hard action socket using the snaprite system. amandrel has been inserted through the center
of the snaprite socket die and then the snapsocket is inserted and pushed onto the die. the quick fit pin socket is removed from thefabric and the mandrel pushed through the hole left by the qfps from the backside. thedie can be snapped onto the existing stud on the boat. using a standard rivet tool with the snapritebutton die screwed onto the nose a snaprite snap button is inserted in the die. the button’sbarrel is pushed over the mandrel and the rivet tool’s handle is depressed severaltimes until the snap is installed. next up we will show using the pres-n-snapinstallation tool to install a snap. unto the socket die a snap socket is pushed anda button onto the button die. now simply position
the snaps barrel over the hole left by theqfps pin and depress the lever of the tool once. the pres-n-snap creates a hole and setsthe snap in one squeeze of the lever. both the snaprite system or the pres-n-snaptool are available from sailrite. before patterning the larger aft curtain the starboard aft sidecurtain must be completed in the same manner as this one. finally we can now pattern for the largeraft curtain. to the zipper at the top which zips onto the awning rope apply seamstickfor canvas 3/8†wide to the side that is facing the bow of the boat. then zip it inplace. now apply 3m strapping tape to the boat as a base for the seamstick that willbe used to stick the dura skirm pattern material
to. now this may seem strange, but brian willplace this strapping tape with seamstick along the edge of the hard radar arch so he canyet again pattern off a solid surface first then he can transition it onto the bastingtape on the zipper once he is happy with the way the pattern looks. this is done exactlythe same way it was done when we patterned the aft side curtain earlier in this video. since we have already shown how to patternwe will show this section in double time. basically cut pattern material slightly large,baste and re-baste, trim away excess pattern material, re-baste until happy.
how’s it look? well, awesome! trim awayany extra then get ready to trim along the top edge just as was done for the aft sidecurtain, so we can join it up with the seamstick on the zipper’s flange. be careful to not remove the pattern materialfrom the bottom edge. now baste the pattern material to the basting tape on the zipper.a helper is always recommended for patterning, though we are not showing that. to keep this corner from coming loose he willapply a run of strapping tape here, just because it is rather small. when we are happy with the way the patternlooks we can start marking the pattern material.
we will mark where the edges, corners, zipper’sstart and stops fall and any other important factors that may impact how this large aftcurtain is made. here you can see brian marking the zipperstop, this is the binding tab that was used as a stop. at the top he marks where the edgeof the side curtain falls and where the zipper pin or post is located for the zipper starter. at the door location he strikes a line thatwill indicate where the future zipper will be installed to allow passage. he does thisalso at the top for the door. a straight line will be struck down at the table or floorlater on. along the bottom edge we will be using thestayput shock cord cover clips to secure the
panel. so our bottom edge will be rather highhere at the stern. if fasteners like snaps or common sense or lift the dot are used morespace would be required to install them. here we are marking the panels for easy identification. as done earlier try to remove the panel withthe zipper still stuck to the pattern material. at the loft table we will strike straightlines where we know they should be, like are at the bottom edge. then along the sides wherethis curtain joins up with the side aft curtain. and at the door. the top edge zipper is still attached. wewill turn the pattern material over and trace along the inside edge of the zipper’s teeth.then at the top edge, since we did not yet
mark the zipper’s start and stop positionwe will do that now before removing the zipper. we need to install a zipper for the door slit.to do this we will measure how far away from the edge the zipper ends at the corner thenduplicate that measurement for the slit at the door. so this will be the stop positionfor the door’s zipper. now the zipper can be removed from the patternmaterial. as done with the first curtain we will placethis pattern under our clear vinyl material and mark the vinyl. let’s discuss the differences in our clearvinyl window materials as brian works to trace around the pattern. you have some choicesin what brand and quality of clear vinyl you
can use. we will start with the best brandsstrataglass and o’sea. these are very uv and scratch resistant vinyls. they are alsovery clear, like looking out a glass window. strataglass is a little stiffer while o’seais softer. o’sea is chemical resistant while strataglass is not. we are using o’sea 30gauge for our enclosure curtains. the second best is crystal clear and regalite both areuv resistant and very clear. crystal clear is more firm while regalite is softer. forthose trying to save money plastipane 30 gauge is an option, but not recommended since itis not as uv resistant and not as clear. remember the cost of the clear vinyl is nothing comparedto the labor involved. everything is cut out and now brian will markthe desired finished size and the cut size
of the facing he wants on each curtain edge.what size do we recommend? that’s coming up next.our panels are ready for the facing to be applied just like we did earlier for the aftside curtain. in general these are common finished width sizes of the facing stripsalong each edge. feel free to modify the finished widths as desired for your particular project.we will make the inside facing from our shelter-rite vinyl fabric in the same manner by tracingaround the edge of our clear vinyl window material matching the shape. this is the topedge and it is curved, however the sides, door slit and bottom are all straight runsso we can just cut strips of our inside facing to the correct width without having to tracethe edges for the shape. the required facing
strip at the top was longer than our vinylfabric so brian is making a second section to be joined to make the correct length forthat top edge section. since we have already gone over how to dothis for the side aft curtain, we will not show all this. however, we do want to showa short section on cutting facing strips for the straight edges, here we will do not haveto trace the edges since they are all straight. cutting our sunbrella outer facing stripsis done the same way, except remember to add a half inch to the width for a single hemalong the inside edge. here we are using the soapstone pencil tomake the sunbrella because it comes off easily. in an effort to save fabric we have joinedtwo sections of sunbrella fabric together
to accommodate the required length neededat the top and bottom edge. after all the facing strips are cut to sizefor the inside and outside surface it is time to baste them to the clear vinyl window panels.since our curtains have an inside facing strip that is different from the outside facingstrip be sure to apply them to the correct side of the clear vinyl. always start withinside facing strips so the outside edge can be hemmed to match.the aft curtain includes two sections, the smaller curtain is the door panel. we willface each of them separately as independent curtains, then later on when the top facingstrip is applied they will be joined together permanently via a zipper and the top facingstrips.
notice that the clear vinyl window materialis being worked on while still laying on top of the white paper backing that it was shippedin. this is to avoid accidently scratching the material while we work on it.brian will attach the facing strips to the bottom edge and also at the door slit. rightnow we are viewing the curtain with the inside surface facing up.now that those inside facing strips are applied we can flip the curtain panels so the outsidesurface is facing up. then we can apply the sunbrella facing overtop of those facing strips, just as we did earlier with the aft side curtain.this time brian will secure the outer edge first before applying the facing strip thatthat runs vertical to this bottom edge.
he will do that to the larger aft curtainalso. then before moving on, he creates the hem along the inside edge matching up thefacing edge below under the clear window. then sew that hem in place. do this also forthe door panel, we will not be showing that. after the bottom edge is finished, we willtransition to the basting on the sunbrella facing at the door slit following that sameprocedure, we will not show all the steps for this either.we will sew the binding on at the bottom edge and the door slit on both our curtain panels.notice that brian is helping to push the assembly through the binder feeder and he is keepingthe assembly pushed up against the binder edge. since this assembly is rather thickif fits very tightly in the opening of the
binder, helping to feed it keeps it feedingconsistently. coming up next we will show how to sew thezipper for the door slit. the panels have been placed over the patternmaterial so the zipper stop position can be marked accurately on the curtains.since this door slit or opening does not need a separating zipper (called a finished zipper)because it will be sewn together at the top we can instead use a continuous length zipper.the panels will be flipped inside up and a length of continuous ykk zipper will be cutto size, slightly longer than the curtains height.seamstick for canvas â¼â€ will be basted to the zipper’s sides or flange.he transfers the zipper stop marks on the
outside to the underside surface. a soapstoneworks great on sunbrella, but a grease pencil works best with vinyl. i do not recommendusing a grease pencil on sunbrella, as it is difficult to remove the marks.with both the main aft curtain and the door curtain lined up perfectly start basting thezipper in place. just in case the zipper moves brian placescross marks along the length of the zipper on both sides. these marks make it possibleto re-baste and sew the zipper down correctly, if it comes un-basted accidently.to separate the zipper just pull the ends apart and run a finger down the middle ofthe teeth. we must be careful to keep the zipper basted in place while this is beingdone.
we are using binding to create zipper stopsfor the zipper ends, this will be the bottom edge. stops are not needed along the top edgeas a facing strip will cover the zipper along the top edge.we can sew the zippers on while the panels are separated and thus easier to maneuver.before reaching the top edge, stop sewing an inch away from the edge of the clear vinylwindow material and do some reversing at this point. keeping the zipper away from the topedge by about an inch or more will make it much easier to sew the top facing in placelater on as we can cut away some of the zipper here.here we are sewing the second panel, and notice that the top edge is where we are startingand we are again about an inch away from the
edge. here at the stop at the bottom edgedo some reversing to lock the stitch in place. now we will finish applying the facing tothe sides of our curtains. the process is the same as any other facing strip exceptthat brian already installed the binding on two edges. so, we will have to end the facingstrip at the top edge of the opposite facing strip and create a pleasing single hem atthat end. watch here as brian completes a hem that lays right up against the facingalready installed at this bottom edge. then before creating the inner edge hem sewthe outer edge to keep it in place. as done earlier this outer edge will have bindinginstalled in a later step. then work on the inner hem of the facing matching it up tothe facing on the inside surface underneath.
here we are working on yet another facingstrip. once the facing is applied to the sides wecan finish off the top edge. to do this we must zipper the door curtain to the main aftcurtain. with both panels side by side, lined them up perfectly slide the zipper slide ontothe zipper’s teeth. we are using a double pull slider so it can be opened from the insideand outside of the enclosure curtains. now the inside facing strip can be positionedalong the top edge. but first we must cut off the extra zipper hanging off the edge.we will cut it off as close to our stitch that stopped about an inch inside the edge.this will make it easier to sew the top outer edge (which will have a binding installedlater) since the zipper is removed in that
area.to save on fabric we made two length of this facing strip, since it was so long and takenfrom scrap fabric. flip the panel and complete the outside surfacefacing strip made from sunbrella fabric here. we will show this rather quickly since theprocess is the same. notice how beautiful our door curtain slittransition looks. when sewing and upon reaching the zipper inthe door, it is best to walk the sewing machine by hand over this area since it is ratherthick and we are sewing through the zipper’s teeth.after the facing is installed, simply install the binding along the top edge then the sides.since the zipper stops about an inch away
from this edge it is easier to sew the bindingon this edge at the door slit. we will use the sailrite edge hot knife tocut any trailing binding off and to keep the ends from unraveling.next we will install the zippers to the sides and along the top. to do this lay the curtainover the pattern and mark the start and stop positions of each zipper at the correct locationson the curtain. we’re using the soapstone pencil to do this.after that is done, we will flip the curtain and work on it with the inside surface facingup. we will apply seamstick for canvas â¼â€ to the flange of the zippers and then bastethem in place. along the top edge we will allow the zipper to hang over the edge ofthe binding so the teeth are almost exposed
completely, as seen here.this zipper is slightly too long so we will cut it off and install a zipper stop, we willuse binding. along the sides we want the zipper to be mostlyburied inside the edge of the binding to protect it from the weather. here is a close up shotof that compared to the zipper at the top edge.these zippers are also slightly too long, they will be cut off and a stop installedas well. brian will also replace the plastic slider for a metal slider which you can seehere. the metal slider slides easier, but it may not last as long in a salt water environment.i have no problems using plastic sliders and in my opinion both plastic and metal haveadvantages and disadvantages, i typically
use plastic sliders in all my personal applications.sew all zippers on following the same procedures outlined in this video. coming up next wewill install the curtain and mark the position for fasteners along the bottom edge.the curtain is ready to be installed and fasteners used along the bottom edge to secure it. thisboat used the shock cord cover clips but often regular snaps are used or common sense fastenersor lift the dot fasteners and other choices are available at www.sailrite.com feel freeto call us up and discuss options, if you’d like.a shock cord lacing knob was already installed on the boat (the lacing knobs available atsailrite are better quality than the ones shown on this boat). brian is simply markingwhere he wants each stayput shock cord cover
clip installed on the curtain.to install these fasteners the curtain is best removed and taken to a work table.in an effort to make installation easy we will use a scrap section of fabric and puncha â¼â€ hole in it with a #0 hole punch from sailrite. this hole should be installed inthe scrap fabric so the shock cord clover clip just hangs even with the bottom edgewhen installed, as seen here. now we can use this templet to install eachhole along the bottom edge of our curtain. using a cutting block like this premium cuttingblock from sailrite will help protect the cutting tool and the work surface below it.as always a heavy mallet works much better than a standard hammer for installing holesand fasteners in canvas.
to assemble the stayput shock cord cover clipsimply insert both ends of the shock cord with metal crimp preinstalled into the openingsinside the cover as shown in the video. we will insert through the hole we just madein the cover the male backing plug. the post is a self-locking system which only take afew light taps of a hammer or mallet to properly install the cover in place over it.let’s move on. only one more task to accomplish, the roll up strap for the door. that’s comingup next. we will reinstall the aft curtain and attachit to the aft side curtains. as with most doors and roll up windows a strap is utilizedto secure a rolled up window to allow passage or airflow. before we can start to make thatstrap we need to secure the bottom edge of
our curtain using the stayput shock cord coverclips. we always suggest using the zipper pull tabs to help aid in pulling the shockcord over the knob, as seen here. those zipper pull tabs are also great for zipper slideras that is what they were made for. ok enough of that, lets show how to make astrap for the roll up door. here we are using a 1†nylon black webbing and using the sailriteedge hot knife to seal the end and keep it from unraveling. we will install a snap withthe snaprite system. the webbing has been folded back upon itself about 2 inches. pushthe webbing assembly through the mandrel that is inserted in the snaprite eyelet die witheyelet snap in position. let’s rewind and show that one more time, with a few more pointers.notice the webbing hem is facing down and
the mandrel is pushed through the webbingnear the bottom of the 2 inch hem, so a second snap can be installed above it.so an eyelet snap is on the underside and a snap stud is on the top side. using thesnaprite stud die installed on a standard riveting tool we will insert the mandrel intothat die and depress the lever of the rivet tool several times until the snap is set firmlyin the webbing. above this snap we will install another snapstud with eyelet. it will be used to secure the webbing when window is rolled up to theaft curtain. since this eyelet will need to go through the webbing and the clear vinylfabric, as seen here, we will need to use an eyelet with a longer barrel length. thiseyelet has a 5/16†barrel to accommodate
thicker assemblies, we will use that here.this time we will push the mandrel through the side of the webbing without the 2 inchhem (this is opposite of how we installed the first snap). then we will take this tothe curtain and position it over the door’s center position (we only need one strap forthis small door, you may need more for your application if your door or window is larger).insert a snap stud into the snaprite stud die and install the snap as done earlier.the mandrel does not necessarily need to break, but if it does that is ok they are expendableand should not be used more than three times over. when installing this snap the mandrelbroke! roll up the door and determine where the snapshould be installed in the webbing. the webbing
should be cut again with a hot knife to thecorrect size and it should include enough extra for a 1 inch hem at the end.we have inserted a mandrel through the snaprite socket die and will install a snap socketonto the die. then in the rivet tool we have the snaprite button die installed and we willinsert a snaprite button onto the die. into the 1 inch hem near center location ofthe webbing this snap should be installed so it will snap onto the stud that is alreadyinstalled on the curtain. the process is the same as what we showed earlier on for theeyelet and stud, except that this is the button and socket snap components.the strap can be snapped inside the curtain to keep it out of the way or it can be snappedto the outside surface of the curtain to hold
up the rolled up door.our aft enclosure curtains are now complete. coming up next is the materials list and toolsthat we used in this video. if you have any questions regarding what typeof clear vinyl window material or about any other products we carry, give us a call atsailrite, we will be glad to help! some powerboat enclosures use a vinyl fabric for the facingsinstead of sunbrella, brands like stamoid or weblon regatta are very popular. if usingthose vinyl type fabrics the construction process is still the same as outlines in thisvideo. videos covering how to make the bimini and the side and front curtains are alreadyposted, check them out at www.sailrite.com or the sailrite youtube channel.
for more free videos like this be sure tocheck out the sailrite website or subscribe to the sailrite youtube channel. it’s yourloyal patronage to sailrite that makes these free videos available, thanks for your loyalsupport! i’m eric grant and from all of us here at sailrite, thanks for watching!