About : standard furniture last call
Title : standard furniture last call
standard furniture last call
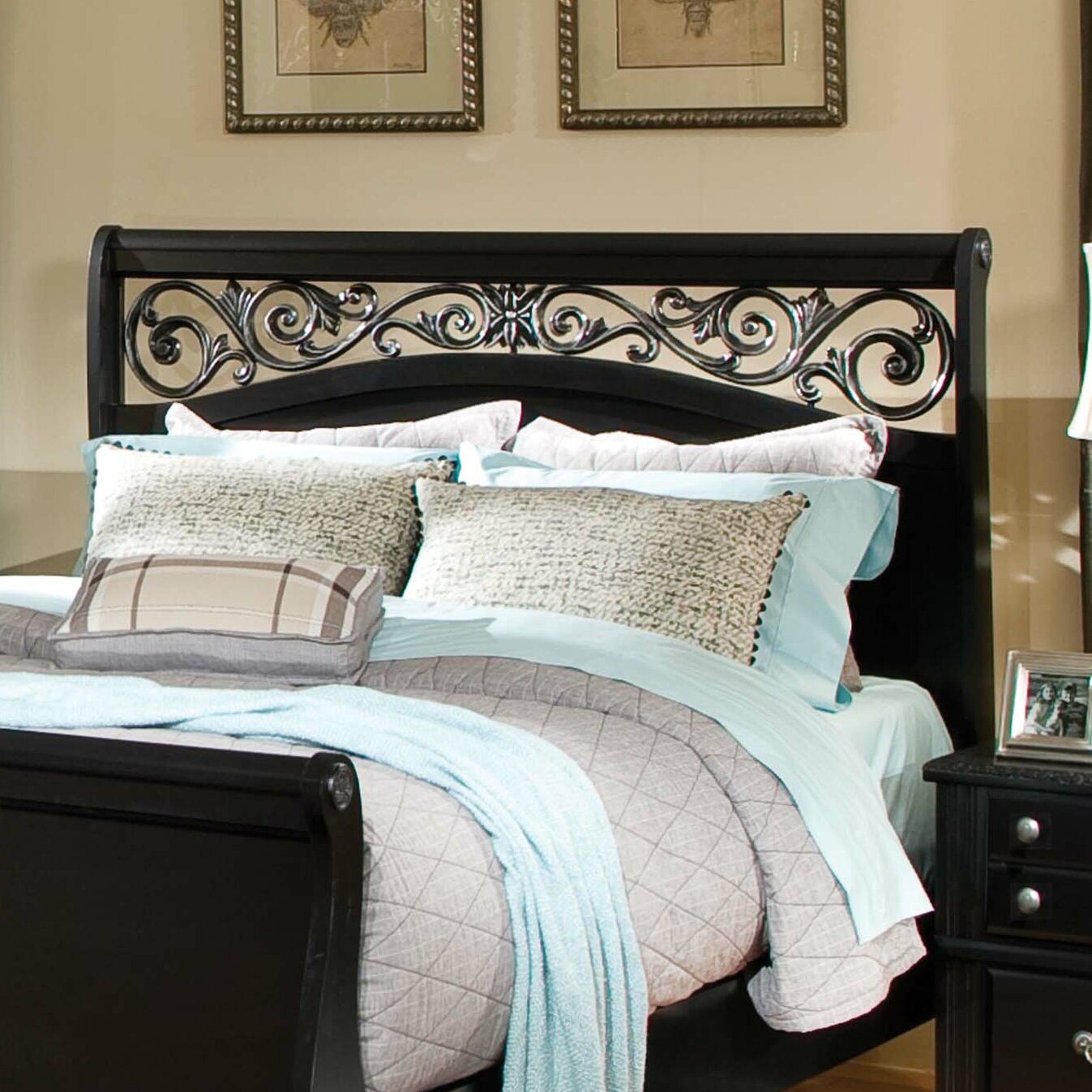
- sure. - oh my arm. - sore still, me too. i'm going to do this beforethe introduction here. oh, poop, get off of there, okay. i think we're live now. - i think we are. - okay. - did i get you the right spray?
- yeah, they're two ofthe same thing, though, but that's fine. okay, well i guess i usually like to get some confirmation, but, i guess after thisfirst part when you go back if they say "it's notworking," then we'll know. - usually, it will say. - okay, are we ready to roll? - yeah.
- should i even ... yeah, should i record the beginning? do i normally record the beginning? i haven't been. all right, i'll just record it anyway. how's my makeup, good? - non-existent. - oh, okay. - how's mine?
- you look fantastic, as always. by the way stick around. after the live sessionwe're gonna have ... well, it will be live, too, but after tww live, we'll be doing a demo on creating a flexible sanding strip, something i get a lot of questions about. it's very easy to do. that's a can of adhesive,
so stick around for that. - i'm guessing that's part of it. - it will be, yes, an important part. so let's get started. this is "wood whisperer live, "tww live," number six. - is it number six? - number six. we're a week late because we were
out of town last week, and had a scheduling snafu. - you know blizzcon. - blizzcon, nerdy stuff,we love nerdy stuff. so, yeah, happy friday. i'm marc spagnuolo. this is my wife, nicole spagnuolo, and we're here to waste some of your time on a friday morning with some cool stuff.
now we will have a couple of giveaways toward the end of the show. make sure that you are either at the "wood whisperer live" page, that's the woodwhisperer.com/livein the chatroom, or you're on our youtube page, and you are participatingin the comments section. that's how you getentered into the giveaway. so, if you're participating and talking,
there's a good chancenicole will see your name, and you have a shot atwinning a couple great prizes which will be at the endof today's live session. so, let's get right into our giveaways. we love giving stuff away. - we do. - so last month ... you do, i do, too. last month we had a nice giveaway. it was the festool ct36 vac and boom arm,
killer combination, who was the winner? - that was donald ell, and,in fact, we met donald. i can't remember when it was, but when we were at weekend with wood. - [marc] weekend with wood, yeah. - [nicole] so, yeah, we met donald, and it just so happened i didn't realize. - [marc] i remember him. - [nicole] yeah, andjust on a serious note,
donald, if you're watching this we want to send out our condolences. he recently lost his father. - sorry to hear that. - we wanted to mention that, and tell him we're thinking of him. - yeah, i know,congratulations on the win. hopefully some new gear or some new toys will help cheer you up a little bit.
okay, so this month's giveaway. - wait, wait, we forgot the second winner. - oh, that's just a guild membership. it's not important. - that's just a guild membership. oh yeah, $129 value. - justin, right? - yeah, justin. - justin won a guild membership,
so congratulations, justin, hope to see you in the guild. - he's already in there. - oh by now? - he used the coupon code. - okay, good. - at least, i hope that was him. - awesome, all right, excellent. so this month's giveaway.
we got a couple good ones here. our friends at arbortech, they've got a new tool. it's called the arbortechrandom contour sander. if you're into powersculpting and carving, you know that you have lots of odd, irregular shapes, and that's what this sander is meant to accommodate because
you just can't get in there with any other type of power sander, it's all by hand. so the contour sanderis a great way to go. some lucky winner isgoing to win that thing. all right, that's pretty bad, eh, as we say for a pg-rating. and what's the other one here? the festool ts 55 and a ct 26 vac combo. - [marc] that's a killer combination.
- [nicole] that's an awesome combination. - that's the combination that got me started on festool. - i do remember that. - i do. - i do remember that, i don't know. - that's how i got her to marry me. she just randomly says, "i do," and my timing was good,
so thank you, nicole. all right, so festool ts 55, ct 26 combo. you can enter to win. just go to thewoodwhisperer.com/giveaway." enter your information there. we don't ask for a lot. we do give you the option to join a couple of mailing lists, and we double opted-in for that,
so we're not just goingto start spamming you, but if you give us your email we are respectful of that, and we don't sell your email to anybody, so, go ahead, enter that giveaway. win some great free stuff. we highly recommend winning free stuff. every month i have new stuff, so next month i'll have another batch
of goodies to give away. the more you guysparticipate in this stuff, the easier it is for us to sell it to big companies and say, hey, give us really expensivestuff to give away," because they get a tonof promotion out of it, i mean, and it's not even something that we make any money on. it's just something that like if we
could make these things happen, boom, here you go! - boom baby! - boom baby, free tools. - free tools. - all right, thank you very much, nicole. - bye. - it was good to see you. - see you in the chat room.
- i'll see you later on. all right, moving on today. by the way it's going to be a fairly quick show today. it's just the way things panned out. so news and announcements. "woodworkers fightingcancer" is still going on, going strong, and we areabout 50% to our goal. now, that's good, and it may not sound
like a lot depending on your perspective. maybe you think wewould be more than that, but the point is rightnow we haven't actually done the tally of all the bills. the big thing that's going to result in a lot of money coming into the charity, so we're already at 50%before the final tally, so this is all the auctions and things that nicole is organizing,
and 50% is a good amount of money. - so i've been doing ... - hi, nicole. - hi, again. - how's it going? - so i've been doing a lot with "woodworkers fighting cancer," and we have been auctioningoff a few things, and today is the last daythat you can bid on the ...
- the benchcrafted. - the benchcrafted vise,it comes with the ... - it's the old leg vise. they came up with a new version, but the old stuff is still fantastic. it's the one that used to be on my bench, so when i disassembled and upgraded mine i'm making this oneavailable for this auction, so really high quality stuff.
you might have to build a couple components out of wood, that's to be expected, but the vise, the screw, the handle, everything is still in that kit. - and it comes with a yearsubscription to the guild, as well as a phonecall with you. - yeah, it would be like, "hey, what's up? "do you mind if i call you
"on midnight at a thursday?" maybe i'll have a couple of drinks before, hey baby! - so, yeah, i just wanted to mention that. - let's talk about wood. - and did you tell themall of the toy chests are at the bottom of the page? - oh, yeah, go towoodworkersfightingcancer.com and you'll see basically a gallery of all
the toy chests that have come in. we're a little delayedin getting them up there, but as they roll in, nicole keeps dropping them on that page, and you can keep track of all of these great submissions. and, again, we're donating money for each one that comes in, so if you haven't got one yet,
go to woodworkersfightingcancer.com, and you get all that information. - [nicole] tell themwhere the money goes to. - oh, yeah, the money this year is going to the cancer research institute. kind of change it up every year, and it's a really worthy cause, so hopefully you willparticipate and join us. all right, what have we got going here?
oh look, there's a lower third. it's very high tech over here. in other news i wantedto send a quick shoutout to our friends over at 360woodworking.com. you know those guys. i love that picture. it reminds me of the three gorillas, the hear no evil, see noevil, something, thing. you know what i'm talking about, right?
360woodworking.com. you've got chuck bender,glen huey, bob lang. that is a heck of a group of guys, and a ton of knowledge that they're going to be spilling onto you, whether you want it or not. yeah, so, "360 woodworking." they just launched, you know, this is interesting towatch this whole thing
roll out and what they'reactually gonna do, because i don't thinki've ever really seen anything like this before. you've got mass exodus from a magazine, and these guys have afire lit under their butt to really do something awesome, so i'm gonna sign up. i haven't had a chance yet, but they have a pretty reasonable
yearly subscription price, and i want to see what theycan bring to the table. they certainly have theexperience and knowledge, and i want to learn from these guys. i always enjoyed learning from them in the magazine, and there are various things that they've done online, so i just can't wait tosee what they come up with.
so go check it out. i'm pretty sure everything is free until the end of the year, so you can kind of see what they're going to be about, how they're going to putthis information out there, and then you could sign up, but you can also sign up today. i highly recommend you do.
support independent woodworking. i think it's a good thing. support the magazines, too. i think that's a good thing as well, but, you know, i'm wishy-washy. oops, wrong picture. okay, so feature viewer project. now we get a lot ofsubmissions for projects on our website at the "wood whisperer,"
and we can't post all of them because we only post a couple a month, so, it is what it is, but you could submit yours if you want to at thewoodwhisperer.com/submit. send us a picture and we'll go through it, and hopefully you'll see it on the website just like mark's sleigh bed. take a look at this beauty.
i'll read a little bitof what mark had to say. his name is mark stubblefield, by the way. he said, "this was my very first 'real' "furniture project. "i started the project when my wife "was about three months pregnant, "figuring i’d get done easily before "my little girl was born. "well, i was wrong.
"my little girl showedup a whole month early, "which delayed the final project until "about six months after she was born. "the whole bed is solid african mahogany, "with mahogany veneer plywood. "the curved portion ofthe front and back of "the sleigh bed were done by ripping "long strips from the same board, "mitering their edges,
"and gluing and screwing them together "to get the general shape." see the front folds down. see if i have a picture of that. there you go. "the front folds down for easier access "and the bed height is adjustable. "it converts into a toddler bed with a replacement front that's just
"a fence to keep the littlelady from rolling out, "and can eventually convertinto a full size bed. "finish is general finishes java stain, "with four or five coats of hvlp "applied general finisheshigh performance poly, "i had a lot of fun building this project, "and once i get some other things "done around the house, "i plan to make some morefurniture in the future
"with all of the knowledgethat i've gained." very nice, looking good. that looks ... like mygrandmom used to say, "that looks as good as store bought." i'm not sure what that means, but look at the little cutie there with the little diaper butt. little babies walking around with these giant butts onthem full of wet diaper.
i love it. it looks beautiful, great project. i couldn't pull thetrigger on building a crib when the time came. part of it was scheduling conflicts, but the other part was just fear. you know, there's a lot ofregulations and concerns, and probably more than we really need. let's be honest, thingsare regulated like crazy,
but i was just a littleuncomfortable doing that. you know, the other thing is, i don't like building temporary projects, projects that will only be used for a short period of time. now mark's solutionthere to do this sort of sleigh bed, multifunctional bed is great because once it turns into a twin bed you've got something that's going to last
for the kid's entire childhood and grows with the kid, so if you're gonna do it, i think that's a brilliant way to go. so, well done, mark, and once again, you wantto submit your projects. just go to thewoodwhisperer.com/submit. send me some pictures,really high quality pictures, and a good story.
it doesn't have to be a high-end project. we like to post basic projects, but i need good pictures and a nice story to go with it and thatincreases your chances of actually getting it on the website. all right, let's move into,in case you missed it, a couple of things to point out, stuff that i found on the web. you may have already seen it,
but here we go. "highland woodworker." i never miss an episodeof "highland woodworker." it's one of the few shows that reminds me of the old tv woodworkingshows that we don't really get a whole lotof anymore these days. i know a lot of folks like to hear ... i don't know, there's a certain charm to the garage woodworker with
a basic camera showing how things are getting done, it'sjust kind of gritty. that's fine, but i stilllike a really well polished woodworking production, sometimes, and that's what the "highland woodworker" is all about. so in this particularone i know a lot of you are going to be interested in this. they take a tour of thelouisville slugger plant,
and actually show how the bats are made. they show how the oldbats used to be made, and then they show the current version which is pretty amazing, so take a look at this clip here. i think you're going to like it. - this is our staging area. this is where we stage all the wood before we turn thatwood into baseball bats.
this is the machine that makes all of our major league baseball player bats. the old-fashion way ofhand-turning the bat which we did for over 100 years would take 15 to 20 minutesto hand-turn one bat. the tracer lathes would take a couple of minutes or so. our cnc can carve a bat,as you can see here, in about 45 seconds.
of course, now it's going to go down the production line and be sanded, be branded, have finish put on it. (mumbling) are sawedoff, the bat is sanded. the cup on the end of the bat takes place, and basically what that does, it's like a huge drill bit that goes in to the very end of the bat, and carves a cup into it.
it takes about a half an ounce of weight out of the bat. - pretty cool stuff, right. 45 seconds to do an entire baseball bat. that's crazy, that is crazy awesome. i think that whole clipwas about 45 seconds, so imagine going from a blank to a finished accurately milled baseball bat in that amount of time is insane.
also, in that episode, chuck bender. i just mentioned himfrom "360 woodworking." this is while he was still dating "popular woodworking,"so it's a little weird to see them together like that, but chuck benderdemonstrating and explaining his method for brushing shellac and charles brock, the host, he checks out the newbenchcrafted classic leg vise,
and installs one on his workbench. now i've got another clip here for you. this one is from mybuddy, matt vanderlist, at mattsbasementworkshop.com. i thought this one was funny. matt makes a beard comb, because if you're not familiar with matt, the man has himself a sort of grizzly looking thing hanging from his face,
and i guess he likes togroom it now and then. so here's a little clip of that. - hey, everybody, welcome back to matt's basement workshop. on today's episode we are making this fun, little beard comb. then it's back over to the table saw where i slide the rip fence to mark, and then remove the material.
now once the comb blade was cut free, i need to clean up thesurface, just slightly, to removed blade marks. once the comb blade ispositioned where i want it, i then add a couple of clamps, and i set it aside to dry. so now it's over to the band saw to start cutting all those curves. i have all that first cut with
the slot on the fence and make the cut. then it's a matter of unclamping, moving the blade over slightly, and making the next series of cuts. so the final steps are slightly chamfering the ends of the teeth, a task which is easilyaccomplished with a chisel. 96, 97, 98, 99, 100. - that's just awesome.
i do have visions of matt sitting in front of like a dressing table in his sleep gown brushing his beard like, you know, classic imagery of womenbrushing their hair. matt is stroking his beard100 in each direction. all right, so the other thing about matt is he is running a patreon right now, so i should remind you about that. it's a way you can support people
who make free content. so go topatreon.com/mattsbasementworkshop. see what that's all about. you get some nice bonuses if you want to participate. matt is one of the early ones, you know, before me, even, in podcasting, and it's nice to supportthe folks who support us. all right, here's one more clip for you.
this is called "saw hero," and i just had to play it because i think it's flipping hilarious. it's not even that long of a video, but this is what a lot of folks have sent this to me, including nicole, saying that this kind of looks like me, a little bit, and this is how they think of me when i'm in the shop.
(upbeat music) - i'm pretty sure theonly word to describe that is "epic," possibly also "accurate." i often do a log roll type action. log roll dancing on topof my table saw blade. i think the best part of it is when he's just with the music cross-cutting, pushing it back and forth, and to make matters worse the blade is
going in the wrong direction, or it's mounted on the wrong side, so hilarious, i love it. now the other thing we've got here. let's move into gear up! i've got a nifty little jig to show you. i don't really have anything to demo with the jig because it's brand new to me. i just got it in and we'regoing to do a review.
now if you're notfamiliar with leigh jigs, those are the guys, if i'm not mistaken, that invented the dovetail jig. and they sort of stillhave what most consider to be the cadillac of dovetail jigs. the d4r is sort of their flagship product, and i've got one, it's fantastic. a little complicated to set-up, but once it's set-up,
man is it a fantastic little device. so they recently came out with a new one called the rtj400, and it's this little guy right here. basically, it's ... youknow how a router jig, dovetail jig, generally you're taking the router to the jig. well, this is the opposite. this is taking the jig to the router.
it's meant to work witha standard router table. now i haven't used itso i can't give you any realistic opinion on it, but we will do a quick review of this. i've got my shop buddy, shop assistant, i guess you would call him. scott is going to come in. he's gonna take a look andput it through its paces, and we'll do a nice littlereview for you, an opinion.
one thing with these jigs that bothers me is i don't use it enough to remember the exact set-up up process, so everytime i go to use it i have to sit down with a manual, and kind of reinvent the wheel, get my brain in the right space, and then set it up properly. what i love about thisis on the handle here
there are some quick reference guides slid in there that actually show you the various set-up stepsthat you might need saving you the troubleof going into the manual. so it's kind of coolthat they recognize that and know that noteveryone is gonna want to keep that manual right next to them for every time they use it. so you've got it for quick reference
and you should be able to get set-up a little bit faster that way. so we'll see what the results are, how it works out. i've got my router tableright over here ready to go, and hopefully next week we'll be able to put it through its paces and see how it pans out,but that's leigh jigs. here's a nice littleimage for you to look at.
get a closer shot of it. mine is disassembled at this point, but you could see with the clamps in place and a board being cut that's essentially how it's going to work. not available yet. i'm not sure when they're releasing it, but hopefully soon. all right, let's do acouple of quick reviews.
now i didn't have timeto read both of these. well actually i've already read one, so i'm not going to have to read it again, but maybe i will just for fun because it's just that good. here's two books that i want to make you familiar with. the first one is "the handmade skateboard" by matt berger.
matt berger, really nice guy. i know him back from hisfine woodworking days. he was actually one of the people who thought we were okay backin the day, back in 2006. he believed in us. he worked at fine woodworking and kind of brought us into the fold there as they were expandingtheir online content, and kind of embraced what we were doing.
at the time not a lot of people were, especially in the oldschool publication arena, so matt, really nice guy, doesn't work for fine woodworking anymore, but he's got his owncompany called sk8 makers where they make awesome skateboard decks. i see pictures on facebookall the time of him holding workshops and teaching people how to build these things.
so here's the book, skatemakers. i did actually get a chance to read this in digital format. absolutely awesome and i haven't been on a skateboard since i was a teenager, but this makes me wantto make my own deck, and actually, you know,go out and break my neck, or at least break my arm. all right, so they sent me the book.
i had a quick chance to review it and i thought it was really compelling, because it's not just howto build a skateboard. it's not a simple how-to book. the book throughout gives you perspective on the skateboard movement, and how it's grown and changed over time, and matt really givesyou just a broad overview of the skateboard communityand how its developed,
and then, at the same time, shows you how to build some basic decks, and really, for folkswho are looking to get into this kind of thing, this is a great resource. i don't think there's a wholelot out there like this. the other thing you'll like about it is on the back cover i'min very good company. i was able to give them a little quote
with my opinion of the book, and right below me you see who that is? i know you can't see it. it's nick offerman, you guys know him. actor, comedian, woodworker, and author of "paddle your own canoe." so, yeah, good stuff, check it out, and i also have a coupon code for you. now here's the thing.
towards the end, that's one of the books we're going to give away toward the end of the live show, so someone's going to win one today. if you don't win one, though, you can use a coupon code. go to springhousepress.com. that's where you could buy the book. 30% off, okay, it's for a limited time.
i can't remember exactly how long. you got some time, but it is limited. 30% off, use code ww1114, that's the date. so wood whisperer 1114, okay. good stuff, 30% off, that's a big savings, and i do recommend you get that, if you don't win it atthe end of the show today. - [nicole] it's just wood whisperer 1114. - yeah, wood whisperer 1114.
- [nicole] ww. - ww1114, ww1114. okay, the other book iwant to talk about is "the furniture bible." this is hardcore, all right. this is a great resource for people who are refinishing pieces. maybe you're building, you know, you're trying to build a reproduction.
you want to know a little more about the finishes and techniques that went into those pieces, but it really, if you're into restoration. now when i think of refinishing i'm like, you know, slapthe stripper on there, and, oh wait, that couldbe taken the wrong way. slap on some stripper and take all the paint and crap off andput a new finish on it.
a very, you know, sort of brute force and diy when it comes to refinishing. that's not what we're talking about here. we're talking about restoration where you get a piece that has some historical value and you need to maintain that value. this is a book that really gives you a lot of information from construction
to finishes and maintenanceand all that stuff, and you don't usuallysee this kind of thing, but the forward i believeis by martha stewart, which is kind of cool. so if you want to read that. also, find out how oneknits while in jail, but yeah, so there's also fixes and glues, and tools, and all types of things. so, if you're into restoration
i think this is a must-have book. it looks pretty good. i haven't read through the entire thing. i just kind of leafed through it, but it's called "the furniture bible" by christophe pourny, p-o-u-r-n-y, perny, i think, is how you might say that. two great books. see, books are still important, people.
you can't find everything on youtube. i'm gonna get a little bit of coffee here. all right, what do we got next? what's up next? oh, a little bit of q&a. i hope you're getting somequestions for me, nicole. not just over there chatting, just chatting with yourfriends over there. we need some ...
so, here's the heads up. i've got two ... i got two in the chamber. i got two questions to start with, and then, if you want to, send nicole a question either by commenting on the youtube page or in our chatroom, and i will do my very bestto answer that question, and we're only going to need a couple, okay, two or three.
all right, here we go. the first question here, is from matthew. matthew york, it's atwofer actually, he says: "i'd be curious to know if there are any particular wood speciesthat marc absolutely loves, and if there are anythat he absolutely hates. also, i would wonderwhat his opinion is on wood-bodied planes versusmetal-bodied planes." all right, so clear that off there.
okay, so in terms ofwood, i like all woods. the great thing about wood is it comes in different densities,colors, grain textures. i embrace that, i love it. so i don't really eversingle out a favorite wood. now there certainly are some that are a little bit more fun to work in terms of how they respond to blades and planes and chisels,
and those tend to be the ones that i enjoy working with, but when i want a certain color effect and i want to see a certain grain type, the fact that the wood is hard to work is kind of a secondary concern for me because my enjoyment of working with it is the fact that i'm working with bubinga. it's one of my favorite,you know, wood species,
but it can be a bear on the blades, and it's hard work, but i don't mind, because i want that wood in the project i'm building. now on the other end of the scale i can certainly say there are woods that regardless of how much i like working with them in terms of them being included in a project,
i just don't like theworkability of the wood. now this is a little skinnystick of wenge, w-e-n-g-e. it's an exotic, i believe it's african. this stuff is splintery, it's stringy. it's very difficult to work. it's really hard on the blades, but as you can see it's got a really nice dark color. so there are projectswhere it calls for this,
and i have a customer who seems to have a love affair with wenge, and continues to torture me with it almost every year, but beautiful stuff. it's just a pain in the butt to work, and every time you work with this, and i know folks who have been around the "wood whisperer" site for a while
know how much i've complained about this. you can't work with it for too long before you wind up with hundreds of little baby splinters in your hand. they're not real painful splinters, but they're just kind of annoying. all right, so, wenge, not my favorite. all right, so thequestion about the planes. what do i think about wood-bodied
versus metal-bodied. - [nicole] who is that from? - matthew york. so i've got a couple of examples here. now wood-bodied planes have a certain appeal to them, i think. i mean here's one frommy buddy scott meek. he makes some beautiful planes. this is ... what the heck is the name?
remember this one, hon, do you remember the name of this one? - [nicole] blum. - thank you, why didn't i remember that, and she did, blum tool. - [nicole] why did i remember that? - why did i not rememberthat, and she did? blum tools, all right, nowthis one is their smoother. what i like about blum tools is
wooden-bodied planes typically have a manual adjustment system, and that's what scott hashere, very traditional. you have a wedge that goes in place, the blade is behind it, and you got to use thislittle tappy-tap hammer to position things aroundto back the blade out. it could be pretty finickyand a little bit tricky. there is certainly a learning curve
with something like this. with the blum smoother, if you are used to metal-bodied planes it's kind of a great hybrid solution because you actually have an adjustment mechanism to move the blade in and out, and they have a very special blade system in there with essentiallydisposable blades. i think they can besharpened a couple times.
so this is sort of themiddle of the road thing, but you still get the benefit, or the properties, i should say, of a wood-bodied plane ifthat's what you're into. so, wood-bodied planes, it's kind of hard to describe, but because they werelighter you tend to get a little bit more transfer of feeling from the wood you're working,
how it's actually cutting. you get that transferred through the body of the plane. i find that a metal-bodied plane it kind of absorbs some of that, and because it's heavier and denser i don't necessarily get as much in the way of tactile feedback from it. and that's not necessarilya totally positive thing.
you can say, "oh, i likegetting tactile feedback," that's fine, but i also like what a metal-bodied plane doesin terms of its heft. i feel like if the wood is fighting me a little bit more i canget through it better with a metal-bodied plane, whereas a wood-bodied plane, because i could feel that pressure i actually have to push my way through it
and it's a little harder to work, so personal opinion. other people may feeldifferently about it, and that's why i do tend to favor my metal-bodied planes. now i've got a little board set-up here. nicole, if you couldset-up the camera for me. actually, i should beable to do it myself here. bear with me.
that's just a simple board here. we'll go with a metal-bodied plane and it's just the smoother. so i'll take a light pass. now what i'm hoping you'll be able to do is hear a difference between the metal and the wood. okay, pretty typical. now switch to the wood-bodied plane.
it's kind of a morehollow sound to it, right. and i can tell you even though i'm getting comparable shavings i am pushing harder. okay, the plane is also lighter, so if i'm used to a metal-bodied plane when i switch to a wood-body, it actually may wobble a little bit more until you get used to the fact that it's a little bit lighter.
i honestly can't say oneis better than the other. it's going to be apersonal preference thing. here's the other thingabout wood-bodied planes that pretty, that are,that is pretty cool. did i just screw that up? what makes them cool is the fact that you can make one. i cannot make a metal-bodied plane, but if i set my mind to it,
and got some goodmaterials and maybe a plan, and saw what makes wooden-bodied planes work well, i could probably buildone if i wanted to, right. the krenov style arepretty well established out there and you couldprobably get some advice on forums or what-not. if you don't want to buy one, you could build one yourself.
that's pretty compelling. a lot of people like tobuild their own tools. - [nicole] compelling. - hmm, compelling, that's something i taught my son to do. he doesn't know what it means, but whenever you say something to him, he'll say, "hmm, compelling." all right, now there is one more question
related that i had loaded up here. let me get to that. it's related to planes. easy to answer right now. john maquire asked:"can you explain how to set a blade depth on a hand plane? i have a stanley plane and it either cuts nothing or it gouges. is there a good way todo the initial set-up?
it seems especiallydifficult with adjusters on both the left andright side of the blade. so, here's the thing. if you're either gougingor not cutting at all it may not necessarilybe your blade set-up. it could actually justbe a sharpening issue. we had this discussion just recently on an episode of "wood talk." someone asked a similar question,
and that's what it came down to. a lot of times these things can be solved by better sharpening. so you may just want to address the blade and make sure you're sharpening ... i don't know, i like to go to 8,000. you can stop a littlebit earlier than that if you wanted to, but the blade has to be sharp.
if it's not sharp you do tend to have that situation where it goes from doing nothing to gouging. the other thing is a lot of people don't realize that when you're running a plane over the surface, a lot of times you kindof need to move it around, and don't be so quick to extend the blade down further.
if it's not cutting on the first pass do a few more passes. move the plane to differentparts of the board because sometimes youhave high spots that are preventing that blade from making contact. if you don't get those high spots down and then you just say, "oh well, i got to pushthe blade out more," that's exactly what's going to happen.
you're going to push down and then you're going to hit a high spot, and then it's going to gouge. so you really do need totake your time with it. the other thing is the wood, right. it really depends onwhat you're working with. sometimes some woodsjust don't plane well, and this is why i really like the hybrid woodworking way of doing things
that i can move frompower tools to hand tools, back and forth, dependingon what the material and my personal desires are, but a lot of times, for instance, wenge, we just talked about this. i'm probably not going to take a hand plane to wenge. i'm probably not evengonna take it to bubinga. i mean, someone probably with more skill,
better sharpening skill could pull it off, but i have no desire to work those really hard, dense, difficultwoods with hand tools, so i move to a power tool solution for it. so the wood itself makes a huge difference in how well the tool performs, but sharpen it and then make sure you are going slow with the process of pushing that bladeout and don't rush it.
now one way, and this is sort of something i've learned from anold charlesworth video is to take a scrap of wood. start with the blade fully retracted, and just start to push it out. now if you sight down the front like this with the plane upside down, you could usually start to see when that blade peeks out,
and what you're really looking to do is take a scrap piece of wood, and just start rubbingit across the blade. you can not only see, but also feel how much that blade is making contact as you push it across, and when it feels even on both sides, and it's also a nice light cut. you don't really want a deep cut
especially if it's a smoother. once you have an even cut on both sides, oh that's good, i'mprobably centered, i'm even. so when i approach the wood i'm not going to gouchon one side or the other. all right, so that's agood first set-up step, but you still once it'sarranged left to right, then you still have to make sure you're protruding as much as you need to,
or if you're making a nice slight cut using a smooth planeback it up a little bit. back it up, back it up. okay, a couple more questions. - [nicole] sorry, i got alot more than just a couple. - oh, shoot. remember, though, we dohave a demo coming up after this so that's why i like to keep the questions a little bit more concise.
- [nicole] the last one i just ... okay, it was about planes, so that kind of fits in with that one. - from bbarefoot? - [nicole] yeah. - bbarefoot, and he probably doesn't want it pronounced that way. "bbarefoot: have you ever restored "older metal planes and do you have any
"tips on restoring them?" i did restore a couple when i first started woodworking. i got a couple of old beat up planes, flea market planes and took a weekend out to try to restore them. they looked good, you know, i got them so that they looked good, but i couldn't really get them
to perform that well, and i may have been at that early stage where i wasn't really sharpening properly, and my set-up skills left something to be desired, so i did. since then, i made room in my budget for purchasing planesthat don't need work, so i'm a little bit spoiledin that regard these days. as for tips for setting up.
i don't have any tips for you, because it's something that i'm not really that good at, and there are so many people out there online who restore hand planes that i'm the absolute last person you're going to needthat information from. so do a couple of google searches. look on some forums.
there's probably a ton of youtube videos on restoring an old hand plane from people who actually love the process. you don't want to learnhow to do something from someone who hates it. i don't enjoy that process very much, but you can find the info out there. all right, let's keep moving. i'll try and get as manyas i can real quick.
justin prange, says, "when should i upgrade to a 15 inch planer "over the lunch-boxthat i have currently?" when should you? when you need it, right. your average lunch-box is what, 12 inches? that covers the vastmajority of what you need. i used to have a 20 inch planer and i downsized to a 15 inch
because i didn't need the full 20 inches. i had all this extra realestate being taken up by a machine that i didn'treally use all that capacity, so it's nice to have it if you need it, but very rarely do i have something that doesn't fit within the capacity of my 15 inch planer. that could probably be said for a 12 inch planer, too,
but the floor standinglarge powermatic units. i think the bottom size you can get is 15, so that's where i ended up. so you may never need to upgrade to something bigger and here's the point. this is one of those cases where if you have to ask the question, then the answer is "no." if you don't know if youneed a larger planer,
then you don't need a larger planer. the day that you know that you do, that's when you do. that's kind of a crappy way to explain it, but that's the truth. if you don't need it, you don't need it. remco smith asked a good question. a regrettable question, i think. "have you ever bought tools,
"but ended up not using them at all?" yeah, i have, and usually they wind up either being given away orsold at a very low price to friends locally. we're talking a while ago. this is something, at this point, i don't really do anymore just because in my brain my idea for what i need done in my shop
is pretty well established, so i don't often make, you know, a bad buying decision. i am pretty well-versed in, you know, in the tools that i'm looking for, and i know what i want and i know why i need it, and then once i get it it's great to have. there are certainly things that i may buy
and i'm kind of disappointed in, and regret it for that reason, but not for a lack of usage. now there is one tool that i have yet to touch in the sixmonths that i've had it, and that's my multi-router. i did finally save up the cash. oh, i'm getting a bad look from nicole. - [nicole] oh no, you're not.
- just kidding. nicole doesn't care what i buy. - [nicole] people are going to think you're horrible to me, or i'm horrible to you. - there's a new porschein the back of the shop that i drive up and back in the shop. nicole doesn't know about it, but yeah, so i finally got a multi-router.
i've always admired them and thought that they would open a lot of doors for complex joinerysolutions as i got more into chair building and things like that. just because of the production schedule of the site i just haven't had time to even use it or even dig into it, so not a regret by any means. i'll get it to it eventually,
but i've had it in theshop for a long time and haven't touched it. okay, let's keep going. "any idea when the guild project "after the sculptedrocker will be announced?" soon, jeff, soon. here's the problem with the guild. like, let me ask you this. maybe you do.
some people are really good at planning, but do you know what project you're going to buildfour projects from now, or three projects from now? that's kind of the way it is with me, and i realize i'm in a different situation because i'm teachingpeople how to do this, but hopefully thatmakes you understand why it's difficult for me to say
what i'm going to be doing in late 2016. so i do my best to populate those things, but i often regret my choices. someone at the door, hon. i often regret the decisions i made because i want to go back and do something different, and i don't like committing too soon. the rocker is a big deal.
that's going to be a big project, so i'm kind of trying tointernalize all of that and what's going to beentailed with that build because it's probably going to run long, so the follow-up to thatone will probably be a fairly light-duty project, that won't take nearly as long to do, but i'll get that up assoon as i possibly can. and if you have ideas and suggestions
shoot them over, too. let's see. "any resources on how tomake wooden drawer pulls "like those recessed ones they sell "at rockler for 10 bucks. "can't find much info on this online." you know, i don't oftenlike to point people to guild resourcesbecause i don't like doing teaser type content, but next week,
actually on tuesdayi'm putting out a video in the guild for thedisplay cabinet that has an oval recessed drawer pull. i don't know if it's exactly what you're talking about, but it might give you some ideas for how to accomplish something like that. if you shoot me an email i could send you pictures of it,
but if you're interestedin joining the guild, it's the current projectthat's showing that. a pretty good video on it, too. it involves some carving. okay, "new subscriber just wondering "how your interest inwoodworking started?" that's ken newton's question. ken, i got started inwoodworking years ago. we bought our first houseand it was a fixer upper.
so baseboards had to be reinstalled and casework needed done,flooring needed done. so i was in this real major diy mode, and as a result, nicole saw that i could use new tools. so she actually went out and picked out a craftsman table saw. so after all these houseprojects were done, i was left there with a nicelittle selection of tools
and nothing to do with them. i caught a couple episodes of "new yankee workshop,"which i had seen before, but also "wood works" with david marks, and that sparked my interest in furniture, and the concept of building things for myself and for the house. so i went in, started using those tools to make some of the things i saw,
and got a couple of plans and started building furniture. that's actually how it all began. prior to that i have always been kind of the type to build something. i used to build animalenclosures for reptiles when i was in college. adam, your question is great, but i don't know that i can answer it.
that's a tough question. "what tool is most important to spend "the money on as a 'forever tool' "and not work your way up?" so what he's saying is, some tools you couldsay "all right for now, "i'm going to get this cheap set of "marples chisels, andeventually work my way up "to a better set."
he's saying, "what toolsare the ones you buy, "the best one you can right away?" you know, if you are init for the long haul, kind of hard to know that at the beginning though, right, but if you do know it there are some tools that you are not goingto want multiples of. so, to me, the goodcandidates for upgrade options are things like chisels because when
i upgrade from marplesto a really nice set it's actually really, really nice to have two sets of chisels. you have one for really fine tasks. you know they're always sharpened. they're never going to be nicked, and you use them forreally important joinery, but we still need chisels for other less elegant things like ...
that's not distracting at all. scraping glue, and, you know, stuff that maybe you were usingreally gnarly materials, so it's nice to have what i call the beater set of chisels. so that's a great candidatefor something like that, but you wouldn't necessarily want to buy the best right away. you would want to work up
and as your skills progressyou buy the nice stuff. so for me the thingsthat are the heaviest, and the things that idon't want multiples of are probably one of the ones that i say "buy the good stuff early." now this may be a little controversial, but i think hand planesare kind of like that, too. if you're gonna get anice smoothing plane, and this isn't necessarily because
the multiple things, and it really comes down to the quality making it easier to work with. a lot of woodworkersget in the hand tools, and like the question we had earlier the guy said he has a stanley plane. well, that can mean a lot of things. we don't know what the nature of the stanley plane is,
but if it's an old beater with an old blade on there, and maybe the adjustmentsaren't real good, somestimes the planeitself can be the problem, right, if it's not tuned up perfectly, or it's not rehabbed properly. maybe the sole isn't flat, and it needs to be flat. so those things can get in the way
of us experiencing how these hand tools are supposed to work, and then you go to a woodworking show and you pick up a lee valley plane, or a veritas, a lie nielsen plane. and you take a few passeson a piece of wood, and you go "oh, my gosh! "this is what it's supposed to do. "all this time i've been struggling,
"and a good portion of my "problem is the plane itself." so, in some cases whenyou go for hand planes, i think an argument could be made to go for a high qualityhand plane early on because you're going to use it throughout your woodworking career, and it will just make your life easier, especially if you're new.
if you don't necessarilyhave a ton of experience with those hand tools i find it much more ... let's just say thelearning curve is shorter if you're learning on one of these versus tuning up a plane and then trying to learn to use it. i'm sure some will disagree with that which is fine, just my personal opinion.
okay, i think that's goingto wrap up the questions. guild projects suggesting a child's bed. mateo will be graduating to a big boy bed. mateo has been in a big boy bed for over a year now, hasn't he? - [nicole] 18 months. - he was in a "toy story" bed for a while, and then nicole bought this,like, raised crazy thing. "a little girl about the same age ..."
yeah, you know what, when he's ready to go toa more mature twin bed, maybe one with storage,or something like that, that would definitelybe a good project idea. thanks for the suggestion, but right now i have to endure this giant, plastic monstrosity that's in there. - [nicole] he has fun with it. - okay, so let's do our quick giveaways.
you got a couple of winners for me, hon? - [nicole] we have one from ... - hold on a second. i just closed down the conversation. send me a quick message because i think you gaveme the winners already. little did you know, that you may be a winner and you don't even know it yet.
what are you typing, a book over there? okay, i know this guy. he's been around forever, and i do not know how topronounce his first name. - [nicole] i think it's john. - j-c-h-o-n does notsound like john to me. j-c-h-o-n paradise. you know who you arebecause you've been dealing with this your whole life.
he's in a tww chat room. he actually is the winner of the book. this beauty right here, "the handmade skateboard," so congratulations, sir. jchon paradise, love you guy. i know you've been around for a long time, so i feel bad not knowing how to pronounce your name,
but i certainly recognize your name. make sure, either viaemail or a private message of some sort get us your address so we could ship out that book to you. and who else? cn craftworks. - [nicole] from the youtube chat. - so from the youtube chat the winner of the guild membership
is cn craftworks. - [nicole] i've already contacted him, and he's contacted me back. - oh, fantastic, congratulations. so we'll set you upwith a guild membership. if you already have one we'll just add a year to your subscription. you'll be good to go. and i'm supposed to say hi to luka
who's sitting with jimmy. so, hello luka, hi luka, how are you? are you enjoying watching a woodworker on your daddy's lap? my son actually doeslike watching me on tv like when i put the podcast on the tv. he's like, "daddy, daddy, daddy!" it's pretty funny. all right, so i thinkthat about wraps it up
for the giveaways, that's done. the next show we're kindof on the fence about it because we're pushing into december now. things are slowing down anyway. and we always do sort ofa holiday extravaganza with a lot of giveaways anda live format like this, so i'm thinking maybe we'll just combine the holiday extravaganza with tww live and do it all in one event.
this may be tww live thatwe push to the evening because we always tryto do that one at night. so it's not so greatfor the folks overseas, but the folks in the u.s. will appreciate having a later time so once a year i think we can afford to do that. so that's probably what we'll do. stay tuned to the calendar and you know our feeds and stuff
you'll find out about it if it happens. let me put up a littlecontact info for you. you can get in touchwith us if you need to. all right, so, of course, thewoodwhisperer.com is our website. facebook.com/thewoodwhisperer if you want to follow. basically, i post a lot of inspirational stuff on there just to give you ideas,
occasionally something funny at wood whisperer on twitter, and in any of the social arenas if you want to leave a question for us or ask us something directly you could use the hashtag twwlive, and that will get the information to us. so thanks for watching, everyone. i'm going to close down.
well, no, actuallyeverything is staying open. i'm going to close downthe recording here, and we're going to start a demo. the demo is on how to make a flexible sanding strip, so allow me to set-upfor a few seconds here. bear with me and we will start the demo. in case you don't know, maybe you're new, or you're unclear
on what we're doing, the live sessions willbe available for viewing immediately after, right on youtube. you could watch the whole thing again. the demo is something that i record, extract out of the live session, and produce a better quality version of it as a podcast, if you will. it goes in as an episodeof the wood whisperer
because i don't want thedemo to be at the end of a long live session. if you want to knowhow to build this thing you don't want to have to sit through 45 minutes to an hour ofme yapping at the camera on this, you know, fun social stuff because you want this information. so, i like extracting it out and reproducing it as a stand-alone video,
and that's the reason we do it this way. i'm probably going to want you on the camera, little lady. and your duties overthere are not as needed. i'm doing the best i cannot to unplug anything. all right. this is a good one. this is one that has been requested a lot. i showed this years ago in the guild,
and honestly i can't even find the video. i don't know what i did with it. okay, i need a razor blade, some stuff here, examples. i am in a really, reallyfabulous mood today, and you want to know why? because my son slept until 7:00 o'clock. we've been getting upat 5:00 o'clock, 5:30 for the past three years,
and my fellow parents outthere with fussy sleepers you know what i'm talking about. it's like a holiday whena kid sleeps until 7:00. here's a danger of having your drink and something else on the table. i almost instinctively picked up the adhesive and drank from it. too bad you can't. all right, let's do this.
so i'm going to beprimarily working here, hon. so after i'm done addressingthe camera we'll do, yeah, i got the thing right here. so it will close-up shots. don't back up, where are you going? where are you going? moving all over the place,what's wrong with you? so a lot of it will be hand here and then i'm going to need to go to the
vise up front to do alittle bit of sanding, but that's after we're done. see, i made this. isn't that beautiful? the mock-up things thati make for this show like the toilet paper andthe stick that one time. nothing but the best here. right, i think we're ready to roll. let's do a little demo, shall we?
all right, so you probably know if you watch "the wood whisperer"that i like to make things with curves. i think curves are beautiful and it's great to breakaway from the straight and square stuff that we typically see, and if you have curves you need ways to finesse the curves.
if you cut them at the band saw, kind of like these examples here. you can have a lot of divots. the band saw blade leavesa fairly rough cut, so it's nice to be ableto smooth those out, and also make it nice and regular, so there aren't anymajor dips and valleys. there's a couple ofways that you can do it. there are oscillatingspindle sanders out there
which work pretty well, but even a spindle sanderas it's going around can create divots. it doesn't create what i would call a regular curve, something that's nice and smooth and continuous. so i find one of the best things to use are these little flexible sanding strips. you've probably seen me use these before,
but what i want to show you today is how you make them. they're so easy and quick to make you could just make them on the fly. no trouble at all. you can make them in alldifferent shapes and sizes. you could see i've got acouple different sizes here, but ultimately the smart thing to do is to size them so that they fit
a piece of sandpaper, your standard sheets of sandpaper. they're 8-1/2 by 11, likea regular piece of paper. so depending on how you attach it to the flexible sandingstrip might help you decide what to do with it. let's say you want to fold the ends up to attach them kind of like i did here. see i've got a little folded area there.
you would need to be a little bit shorter of the full length of a sheet here so you have room to bringthat little extra bit over. also, the width. maybe you want to havea perfect half sheet, and that way each timeyou get a sheet of paper just cut it in halfand you know you've got two sheets for yourflexible sanding strip. now for me, i find the ideal size
is actually a little bit less than half. if the thing is too wide it kind of gets uncomfortable to use because most of the time i'm using it on edges like this, so if it's a really,really wide one like this i just don't find thatit's comfortable, right. so generally, i guess youcan call it "general use" i like one that's about four inches
by the full 11 inches and will hold it on to the piece of material here using one of these sprayadhesives like this. so let's make one. i got to get some glue, sorry. hopefully my ca glue is notsolidified in the bottle. we will find out. all right, let's get a shotdown here of this board. got it?
yeah, you can stayright in this area here. all right, so here are the two examples you could see really, really simple. you've just got a flat piece of material that's fairly thin and hassome flexibility to it. the thinner you go themore flexibility you have. now this is a sheet good. i think this is like an mdf core, very thin mdf core ply.
this is actually solid wood. it's quarter sawn white oak, that i drum sanded down. it's very, very thin soit's nice and flexible with good springback, but because the grain is running this way, and it's really thin, over time look what can happen. see i've got these cracks in there.
that's a darn shame right there, i'll tell you that, but, you know, it still works. so over the years i've kind of started to favor sheet goods for this because they really dohold up quite a bit better. but look at the structure here. there's just not a lot to it, right. you've got the flat board.
you've got some handlesand that's about it. so, let's make one. i've got two examples here. one is quarter inch mdf core plywood, and what i wanted to show you is that this thickness that'sa little heavy, right. try to flex it it's notreally going anywhere, and even if you have ashallow curve like here you can probably flex to the curve,
but i got to put a lotof pressure on there to get that to work. okay, so quarter-inch, you might think it's thin enough, but generally speakingquarter-inch it's a hard sell. i don't know that i woulduse that for one of these. so i have a sheet of eight-inch plywood. eight-inch is much easierto bend, nice and flexible, and these are perfect.
so this is the materiali would recommend using if you're buying a sheet good. if you're using solidwood you may need to go to an eighth or even a little bit thinner to get the flexibility you need. the thinner you go, themore flexible it will be. the other thing you need just some scrap stock for handles. the dimensions aren't critical.
i'm sure someone who's, you know, smarter at design than i am could come up with a really comfortable ergogenic handle, but honestly i don't really care. these work just fine. all i would do is ease the sharp edges so that it's a littlemore comfortable to hold. the other thing you should consider doing
is putting a layer of cork on it. now this is just a roll of cork. i got a whole bunch of this stuff that i bought from amazon. it comes in a big roll like this. that's a great base for this thing because if you have justthe sandpaper on wood it's hard to describe, but the feeling isn't quite as good
as when you have a littlebit of a soft layer with some give between the sandpaper and your flat backing, right. so we're going to basically, essentially make a sandwich starting with the plywood and the cork. so here i've got some spray adhesive. this is 3m super 77. for this part this is apermanent installation.
you want to make sure that this cork doesn't go anywhere, so it's not a bad idea to use the highest tack you can get, and i believe there's the super 90. it has a little more tack than this, but for the sake of getting this demo done we will just use this stuff. okay, a little bit on there.
a little bit on there. now, normally you're supposed to give this like a minute to set-up,if i'm not mistaken. just to make sure everything ... it's kind of like contactcement in that way. you got to give it a little bit of time, but let's rush it. - [nicole] you also haveto be 18 to buy that. - [marc] you have to be18 to buy that, really?
that's weird, what arekids using it to get high? nice. - [nicole] no, it's not nice. - [marc] i mean that in a sarcastic way. all right, so that is pretty well adhered. so just grab a razor blade. a little box cutter, x-actoknife, whatever you have, and cut along the edges. really, you get carded for that?
that's very odd. okay, so cork applied. we now have a nice surface. it's got a little bit of flexibility. cork is really the perfect material because it still has enough density to be nice, smooth, and consistent, but also has just enough give to make it more comfortablefor operations like this.
okay, so that's done. now let's attach the paper. it's going to go something like this, and it's a good idea to havemultiples of these, too. you can kind of do twoat once if you wanted to. ideally, you're goingto want to be able to take this paper off at some point, right. the paper is going to wear down. you don't want to haveto build a whole new
flexible sanding strip for that, so if you can, you may want to use the lowest tack material you could find. i don't know if they make something with less tack than this super 77. if they do, that's thestuff you want to use. if they don't, here's my solution. just use a little bit. the other thing you may consider doing is
possibly putting somepacking tape on here, then put the spray adhesive and i think the bondbetween the packing tape and the paper won't be as good as the bond between a porous material like this. so there's other ways youcould really make this a little more efficient or better. i'll do it this way, but essentially you want to be able
to take that paper off again some day. and if worse comes toworse, you rip the cork off, and you start over with more cork. okay, so with that attached let's make sure it's decent coverage here. once again, cut off the excess. now handles. ca glue is really all you need here, but if you've got the luxury of time
you could certainlyuse good old wood glue. i do not have the luxury of time, so i'm going to try to usethe ca glue, it it let's me. here we go. a little bit there. this stuff is going bad, it's getting really thick. okay, and i've got aquick set activator here. just drop it in place, put pressure down,
spread the glue around. use my other hand to do the other side. okay, give it a coupleof seconds to set-up. i see someone in the chat is mentioning loctite's light duty. i also have loctite, butmine is the high performance middleweight bonding. so that may not be whathe's talking about, but you should be ableto find in various brands
whether it's 3m or loctite, you should be able to finddifferent options there. so once those are attached, you should be able to test it out and see you've got a goodamount of flex there. i'm getting a little bitof separation of my paper, but that's all right. i might have wanted alittle bit more adhesive. then again, i'm rushing this,
so things may not be bound as well as they should be. so let's head over the viseand do a little sanding. i'm going to put the laptop on the floor. and here i've got acurve that's been precut. where's my little sander? and the idea here is by putting pressure in the middle you basicallyconform to the curve, but because this has alittle bit of rigidity
on its own it conforms to the curve, but it does so in a regular fashion that ignores the low points. it doesn't follow the low points kind of like using a large bodied plane when you're planing a surface. the bigger the body is the more it ignores those low sections and ultimately creates a straighter surface.
in this case we're not going straight, but we are trying toproduce a regular curve and getting rid of those high points. so using this is just aseasy as it could possibly be. put pressure in the middle, you want to grab the back, put your hand on the front, and you're sort of flexing it as you go. you can go as fast as you want here.
it's pretty fine. normally i would go with a little bit more of a more aggressive paper than that, but you could see it'salready starting to work, and what i'm going todo just as an example, one of the tricks i love to do with this is take a little bit of pencil and you just mark lines across. it's a little harder to see on
a piece of plywood like this, but you get the idea. okay, and now start your sanding. okay, and as you lookclosely at the surface you will start to see areaswhere the pencil remains. i've got a little spot here. there's another section right here. there's a couple moreat the front and back. those would probably go away with
a little bit more work, but this helps you identifythe spots that are too low, and sure enough, run your finger down. you'll actually feel those divots that match what you're seeing, so it's a combination ofusing the pencil marks and your fingers to tell where there's irregularities in that curve, right. and on this side i've got a much more
tighter radius and thisjust goes to show you that there are limitations to this. if the material is too thick, maybe it doesn't bendwell enough to that curve. in this case, there's apretty good curve on here, but because this material is thin, check it out, boom, it conforms right to the shape of that curve. you can't really ask for better than that.
there is a limit again. if this were a tighter radius i probably would not be able to use this tool to get the job done, but for now for this curve, even though it's prettytight it still works, and we should be able ... you kind of have to move your hands in different ways to getthis to work sometimes,
especially in a case where it's really a small curve like this. just hold the middle, keep the pressure down in the center, go back and forth. most of the time your goal is not to change the curve. you don't really want to change the dimensions of the curve,
you just want to smooth it out. and a flexible sanding strip is definitely one of the best ways i know to do that. all right, so you can see that the paper is kind of coming off a little bit. it's not going to go anywhere when i'm actually using it, so that's a good thing because when it's wornout i can actually just
peel it off and go with a new piece. again, this is probably a little looser than i would normally like, but it certainly is getting the job done if i can get it back on there. all right, typically i'll keep these with 80 grit, 100 grit, maybe even 120 grit. it's not usually something that i put finer grits like 180and 220 because usually
i'm trying to shape thesurface a little bit to smooth it out, so the lower the grit, thefaster that's going to go. i don't want to make it take longer, and then once i have thecurve nice and regular i've got other ways that i could sand it to make it nice and smoothup to my final grit, but quick, easy to make. i was on an episode of "rough cut"
that's actually going tobe airing on pbs this fall, and we had some curves to do, and one of the things we needed to do. we pulled the spokeshave off the shelf. we were talking about different options and i said "do you guys ever use "flexible sanding strips?" i guess they don't, so quickly on the fly with materials we had laying around
i made one right there on the show. it just goes to show you, you can make them on the fly. technically they're disposable, but if you put a littlebit of thought into them you can actually reuse these indefinitely which is a great idea. all right, so that's about it. flexible sanding strips.
i don't do a project thathas curves without them. i highly recommend you make one. if you have improvements on the design let me know about itbecause i've been using this basic set-up for a long time and i know there's waysyou can improve on them for people who are much smarter than me. all right, thanks for watching. you guys got to see the behind the scenes
addressing the way i usually address recorded shows. all right, so that's it. do we have enough time to answer a couple of questions? it's quarter after 12 here. we're probably short on time, aren't we? - [nicole] yeah, but we have one here. i'll send it to you real quick.
i'll send you questions thatare relevant to the topic. - oh, the laptop is down there. because you have to go, right? or don't you? - [nicole] i don't thinki have to go, do i? - [marc] i don't know. i thought we had something. oh, it was the rug thatwe were concerned about which hasn't happened, has it?
- [nicole] right. - okay, james phelps. "what else can you use ... "what else can you useif it's a tighter curve, "thinner material, or a different tool?" well, yeah, thinner materialis definitely one option. the problem is you have sort of diminishing returns on that. the thinner it getsthe more fragile it is.
the other thing that you can do on tighter curves is to actually use one of these sideways, and i've done that before, trying to get as much flexas you can going this way. the shorter the thingis the more it's going to be able to follow those curves, but it's not also quiteas flexible that way, so it's kind of hit or miss.
a spokeshave is a greattool to have around. it it's finely tuned andthe wood is cooperating you can actually use thatto smooth the surface. rasps are also a good alternative. - [nicole] did you say scraper? - yeah, a scraper can be used too. a card scraper is good. not your big cabinet scrapers like this, but your standard cardscrapers are pretty good
for getting into those curves, but, you know, a lot of these solutions, if they fit into those curves, it also means for the most part follow your dips and valleys. so if you're using somethinglike a card scraper you need to be very aware of where your high spots are and tryandm try to eliminate them because just kind of blind.
the thing about the flexiblesanding strip is it's blind. you can kind of just go into it and look at the results afterwards and trust that the surface is producing the curve you want. a lot of these other tools don't do that. you can accidentally makethe problem even worse if you're not careful andyou take too much away. pretty good?
all right, well hey, thanksfor hanging out with us on another wonderful friday. i hope you guys enjoyed this. - [nicole] i got one more. - okay, one more, one more, we'll do one more. don't i have to spray this thing to clear up the nozzle? okay, hit me with it.
he says "you could makeyour own thinner plywood "by gluing veneers together." that's a statement. that is correct, sir. - [nicole] i thought he said, "can you?" - that is correct. all right, well thank you, once again. nicole, you want to say goodbye? - [nicole] sure.
- we appreciate it. hope you guys enjoyed this, and we'll see you around the holidays. it may be a little bit ... well we have no reason we can't do the first friday in december. it just might feel a little early to do a holiday thing? - well we always do our holiday episode.
- in december? - in december. - it will be in december,so i guess that counts. okay, all right, well thanksfor watching everybody. i really appreciate it andhave a wonderful weekend. - peace out, all right. i guess i should stop broadcasting so people don't have to watch me finish my coffee.
all right, see you, bye.