About : standard furniture ratings
Title : standard furniture ratings
standard furniture ratings
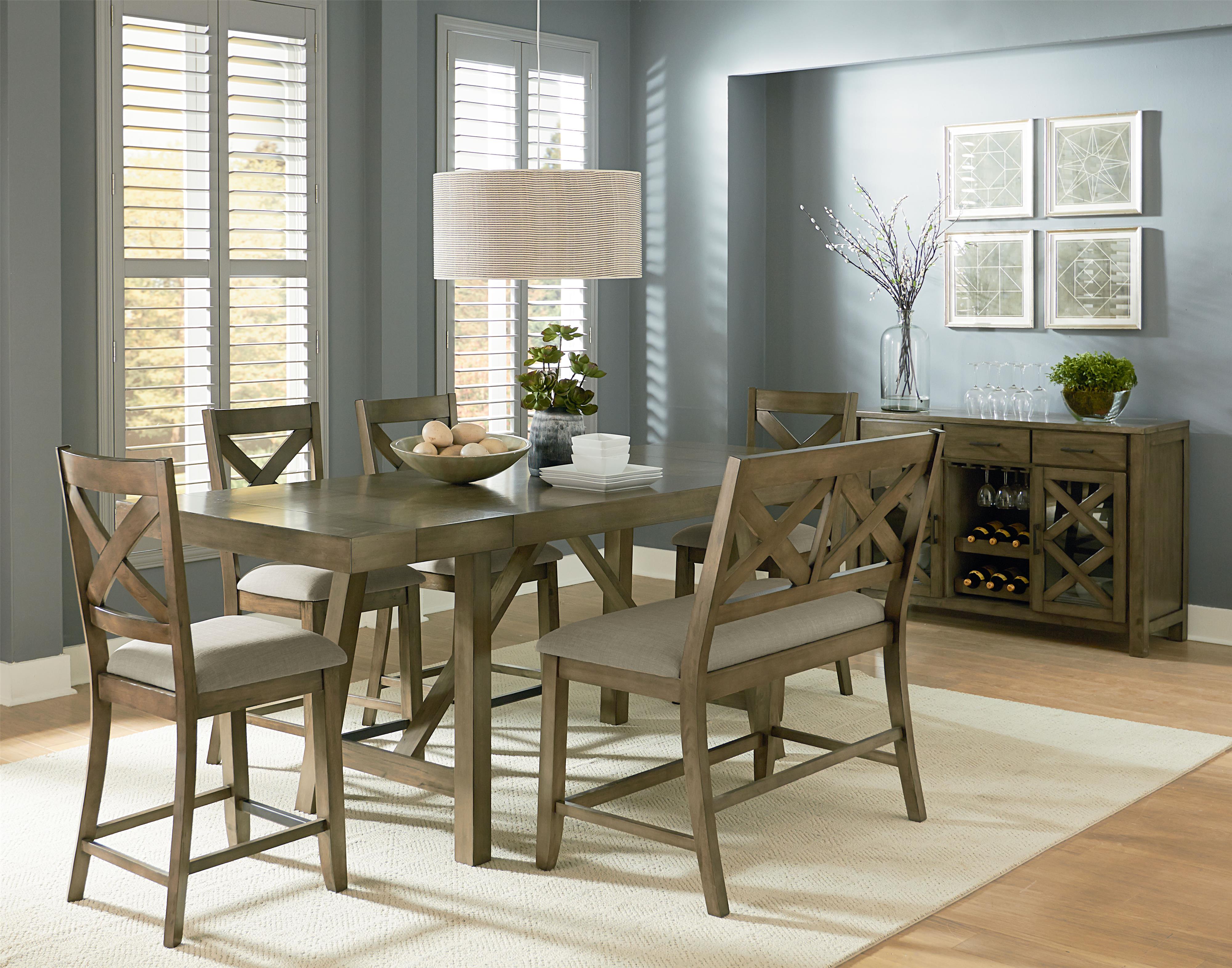
(lively music) voiceover:the woodwhisperer is sponsored by powermatic, the gold standard since 1921 and by rockler woodworking and hardware, create with confidence. marc:pretty much every waythat i know to make a tenon results in a tenon with square edges. now if you make yourmortises with a router that means you are quite literally
trying to fit a squarepeg into a round hole. usually we just dug nearthe corners and it fits okay but what if we could makesquare holes to begin with? well, that's what a hollow-chiselmortiser is all about. the hollow-chiselmortiser makes quick work of the repetitive task of making mortises. within seconds you can produceperfectly square mortises in any species of wood. now this beautiful behemoth over here
is my powermatic 720 hd. frankly it's a little bitoverkill for most shops but if you run a pro shop, you know as well as ido that time is money and if you've got 50 to a100 mortises to batch out, you're going to be thankful that you've got a machine like this. the operation is fairly straight forward. you've got a nice flat table
and a head that moves up and down and drives the bit into the work. in fact it's very similar to another tool that most of us probably have in our shops and that's a drill press. the key difference herethough is the bit itself. the drill press is justrunning a straight circular bit into the work and creating a circular hole but somehow we're ableto create a square hole
here at the hollow-chisel mortiser. the magic is the chiseland bit combination. let me show you whatone of those looks like. this is a one inch chisel and bit set and frankly this is bigger thani've ever needed in my work but it came with the mortiser so i've got it for demonstration purposes. we've got a four sided chiselhere with an ogre bit inside. pretty standard as far as ogre bits go
but it's sized perfectly to fit inside the four sided chisel. now the machine is goingto be spinning this bit and it removes a circularcolumn of material and then the chisel comes up behind it to square everything off. what might be a little bit of a surprise the first time you usea hollow-chisel mortiser is the fact that it'sreally your manual power
that's driving thischisel through the wood. the harder the wood, typicallythe more difficult it is to plunge down into the work. because all the machine is doing is removing a single column of material but when it's all set and done you get a relatively clean mortise. in fact here's an example of a mortise cut with a hollow-chisel mortiser.
if we open this up, you'll see on the inside,it's not a super clean wall. it's certainly not as clean asyou might expect with a router but it doesn't necessarilyneed to be absolutely perfect and the better you set this machine up, the cleaner this wall is. down at the bottom you'realways going to have a little bit of [smuts] down there because just the way the machine is built,
the chisel and bit, the way they work together, you're always going to have a hole that's a little bit deeper and some extra material behind it that the chisel just missed. basically when your set your depth, you take that into account and you can always comeback with the chisel
and remove some of this extra material if you want to get a little bit more depth out of your mortise. mortisers come in twodifferent form factors. benchtop and floor-standing. benchtop versions aregreat entry level tools that will get the job done most times. the problem is they can bea little bit underpowered on some hardwoods
and the tables and fencesare not quite adequate for larger work pieces. benchtop mortisers rangein price from 250 to $450 and they typically support half horsepower to three quarter horsepower motors. floor-standing versions are more expensive than their benchtop counterparts but you get a lot more for your money. heavy duty construction, more power,
larger moveable tables andbetter clamping options make all the difference in the world. they range in price from 800 to a $1,000 with some heavy dutymodels going over $2,000. in most cases they rangefrom one horsepower to two horsepower and that's plenty of power for even the densest hardwoods. when shopping for a hollow-chisel mortiser
whether it's floor-standing or benchtop, there are some key featuresthat you should consider. vertical travel basically means how far up and down thehead of the mortiser can go and of course more travel means that you can fitlarger work pieces underneath and you can make deeper mortises. a depth stop is vitally important in making sure that yourmortise is an even depth
all the way across so that each time you plunge down, this stop bottom is out and it make sure that thebit doesn't go any further than you want it to. if you can, try and find one that has measurements on the side and that actually makes yourlife a little bit easier. a good clamping systemis incredibly important.
obviously we don't wantthe work piece to move. that's kind of a no brainer but what most people don't realize is after your plunge into the work, when you try to pull that bit back out there's a lot of friction there and you can pull thework piece up with you. if you don't have good clamping pressure, that's definitely going to be an issue.
sometimes you may seeunits that have two fingers that clamp down on thetop of the work piece and they are there specifically for that to help resist the work piece rising up as you pull the bit out of the work. built-in stops are areal nice luxury to have. this way you couldregister your work piece up against the stop and know that you're registering
in exactly the samespot every single time. with the arm on the mortiser, there's a couple of thingsthat you want to consider. first of all is the lengthand the shape of the handle. some have a nice sort of l shaped handle which is a little easier to grip and some come a littlebit shorter than this. the thing is, it's all about leverage. the longer the handle, theeasier it's going to be
to pull down into the work. another thing you wantto consider is the angle. is there an easy to adjust the angle because depending on the work piece and the range of motion that you need, sometimes having the handleall the way back here is a little bit inconvenient. it's very hard to reach that. on this particular model wecould pull the handle out
and adjust it to a preset stopthat's a little bit further so this way you have anice range of options no matter how big the work piece is and no matter how deep your mortise is. now one feature that's really nice to have but you typically only findit on the floor-standing units is either a tiltinghead or a tilting table. in case you ever need tomake a mortise at an angle. now this particular model
uses the tilting table option. let me show you what thatmechanism looks like. i've got a full range ofmotion from 45 degrees one way to 45 degrees the other way. once you have the angle you want, you lock down the first lever and then lock down the second lever which is more like a security lock to make sure nothing moves.
now another killer feature that you're really only goingto find in these larger units is either a movabletable or a movable head. the reason we want thisis primarily speed, convenience and accuracy. if you don't have that, you have to unclamp the work piece, move it and then clamp it back in place and then finally plunge down again
and you sort of repeatthat process over and over. with a movable head or a movable table, you're just pulling on a lever or turning a wheel to adjust the position of the work piece relative to the chisel. you can move a lot faster and it's a lot more accurate but again it's really onlysomething you're going to find on these bigger machines.
now in my mortiser, the head is what moves and this lever on the side moves the head front to back. this big monster leveris what moves the head side to side. we also have adjustablestops that you can move one way or the other to limit the motion from side to side and front to back and this allows you to have aperfectly repeatable mortise
no matter what the dimension is. now if you want consistentand repeatable results with your mortiser, youhave to set it up properly. i'm going to show you how. the first order ofbusiness is to make sure that this chisel is runningstraight and through. we want to make sure that the table is perfectly perpendicular to the chisel in the side dimension
as well as the front to back dimension. let's test those separately. first of all side to side and you could see i'm alittle bit out at the top here and frankly i wouldn't guess that that's because i was justmessing with table tilt. it's a very easy fix. i'm going to keep thesquare up against the chisel and slowly tilt the tableuntil there's no more gap.
looks good, tighten it up. now for front to back measurement, just put the square up against the front or the back of the chisel and really we're focusingon this bottom portion here. some of these chisels tendto bow in a little bit especially where thechip ejection slot is. i'm really only concernedabout this bottom half inch, three quarters of an inch or so,
that looks pretty much dead on. now if it wasn't, youhave a couple of options. our table here actually hasan ndf auxiliary surface. it's kind of a sacrificial surface that can be replaced if need be but we can also take the screws out and put in very, very thin shims. you might even just use acouple layers of masking tape to tilt the table one way or the other
and that could very welladjust for any discrepancies that you see front to back. now a more permanentsolution that's going to vary from brand to brand and model to model is to potentially shim theentire top portion here so you might be ableto loosen these screws and add maybe little automotive shims, little brass shims to get the top to tilt inthe perfect orientation.
now of course we can'tforget that the fence needs to also be perpendicularto the table surface. now one of the most commonthings that people mess up when setting up their mortiser is the relationship ofthe bit to the chisel. a lot of people will justput that bit right up into the bevel of the chisel and what that does is it createsa lot of friction and heat. eventually you'll wind up justsnapping these sharp points
right off and you'll dullyour bit very quickly. that extra heat is justnot good for metal, not to mention if the wood is hard, it's going to be nearlyimpossible to plunge this down. what you really need todo is have the bit lead the chisel a little bit. it has to protrude just a little bit. this is not really an intuitive thing so when you set it up at the mortiser,
you got to know exactly what to do to make sure that the bitis in the exact position that you want it to be in. let me show you the tricksto making that happen. just as a safety precaution,it's always a good idea to wear a glove when you do this because you're going to betouching these sharp spurs and little points of the chisel here and that can very easily puta hole in your fingertip.
you don't necessarilyneed two gloves for this, you can just go michael jackson style and i think i just dated myself. the ogre bit is held in with a pretty standard drill press chuck. i could just loosen that up. you'll see that the ogrebit just slides right out and what you'll notice is that the bit is held separately from the chisel.
the chisel is held in this area here and the bit is held by the chuck. we're going to use that to our advantage to make sure that they are set in the proper relationship to one another. now to loosen the chisel,i just use an allen wrench and there's a little set screw in here, and the chisel pops right out. i'm going to reassemble everything now
and we're going to calibrate it as we go. push the chisel and bit all the way up. of course you want tomake sure that the bit goes into the chuck and that your chiselgoes into this collar, this little sleeve here. the trick to making this work properly is to put a little bit of a gap between the chisel and the sleeve
and you'll see how thisresolves in a little bit. that gap is going tobe exactly the distance that we want betweenour chisel and our bit. if you don't have littleshims or filler gauges that you can use for this, you can even use a card scraper. it's nice, it's metal, it's fairly thin. this is about a 16th of an inch. if you want to go a littlebit thicker, use two of them.
i'm just going to use oneas a 16th of an inch shim and i'm going to put it right on top of this chisel's shoulder right here. then i want to push it all the way up so it holds the shim in place, everything is up as far as it can go and that shim is wedged in between the chisel and the collar. now while holding everything in place,
use your finger or if you wantif your fingers are hurting, use a piece of scrap wood to make sure that that ogre bit ispushed as far as it can go, and then we're going totighten the bit in place. once the bit's locked down, you can remove your shim. here's where the magic happens. the gap that's up here,that's 16th of an inch gap gets transferred to the bottom
as soon as we push the chisel up and now that bit is leading thechisel by a 16th of an inch. all we need to do is tightendown the chisel in place and now we have the exactdistance that we wanted between our chisel and the bit. now the chisel to bitdistance is something that is actually going to change depending on the size of the bit and the hardness of the wood.
there really are no hard and fast rules but i do have somegeneral guidelines for you that should help you getstarted on the right foot. (billie jean music) in softer woods things likepoplar, pine, alder and cherry, use a 1/32 inch spacer when using a quarter inch to three-eighths of an inch chisel. if you're using a halfinch chisel or larger,
use a 16th of an inch to3/32 of an inch spacer. in harder woods like oak,birch, maple and some exotics, use a 16th inch spacer whenworking with quarter inch to three-eighths inch chisels. if using a half inch chisel or larger, use a 3/32 of an inch to an eighth inch spacer. many times you can tell just by looking whether the chisel is setup properly.
this one is, this one is not. good, bad. bueno, no es bueno. now the next thing we need to setup is the orientation of the chisel itself. we want to make sure thatthe front and back phases are perfectly parallel with the fence. if they're not, what we wind up doing is getting slightly skewed square holes.
in fact i want to do a test cut here because i know that thischisel is out of alignment and i want to show you what it looks like to sort of exaggerate that problem so you could see how awful that would be on a finish piece. you could see what it creates is this sort of stepped pattern is each time we plunge,we're slightly skewed.
this is really not going to provide a very good fit for your tenon. let's set this up properly so we can get perfect results. first things first, wewant to loosen the chisel and don't worry aboutthat height adjustment that we made before, that'sstill going to be intact as long as this chiselis pushed all the way up, we don't have to worry about that.
we're free to sort of move the chisel back and forth this way until we find the perfect orientation. now some folks and mostsetup procedures i've seen usually recommend that youuse a jointed piece of stock between the fence and the bit. you want to basically just move the head or move the fence so that the bit is right up against the work piece.
you could see i have to movemy little lever back here. until there's no play left back and forth. you see, i can't even really move it. at that point, you want to tighten it down and that should be prettydarn close to perfect but for me personally,i actually like to use the fence itself becausethere's some variability in here if this face of this board was not perfectly parallelto its other face,
you could get a littlebit of a skew there. i like to use the fence itself. to do that, i just bring the head back or your fence forwardif your fence is movable and you see i kind ofrotate it back and forth, do the same thing i did with the wood only i feel a little bit more confident when i go metal to metal like this. getting closer and here at this point,
you could see i don'thave any more movement. now i'm not putting a lot of pressure because i don't want to bend anything. i just want to make sure thatthere's no movement there and at that point we can tighten it up. now we can see since there's no play here, we know that this chiselis perfectly parallel with the fence. that's exactly what we want.
let's do a test cut. there you go huge difference between the first cut thatwe did and the second cut. now i never expect thosewalls to be absolutely perfect but that's probably aboutas close as you can get now there is one more aspect to setting up the chiselthat you need to think about and that's the orientationof this relief slot. this is where all the chips come out.
the reason i didn't talk about it yet is because it's pretty muchtied into your personal method for how you approachmaking these mortises. from the way i see it, there are two ways. i'm going to show you both ways but one of them is a little bit more, well let's say it producesbetter results in the work but it's a little bitharder on the tooling because you have a littlebit more heat build up.
the other method is a littlebit easier on the tooling because there's less heat but you may wind up withslightly lower quality results. let me show you the two methods. the first involves plunging into the wood and making subsequent cuts, one chisel width at a time. by orienting the relief slot toward the area that's already been cut,
the chips eject easily and you have less heat build up. the problem is that duringeach one of these cuts, the chisel is unsupported on one side and it has a tendency to deflect. the second method is what icall the no deflection method. i start by making a cutat each end of my mortise and then stagger each cut there after leaving a littlebit of connecting material
in between. each time we plunge, the chisel is supported on all four sides and will not deflect at all. the remaining connecting material is easy enough to remove. now i'm definitely in favorof the no deflection method. the bottom line is whatever gives me the bestresults for my projects
is what i'm going to use even if it means that i'm putting a little more wear and tear on my tools but also keep in mindthat the other method even though it seems likeit's better for the tool because it's not building up as much heat. that deflection that occursif there's no support on all four sides of the chisel, that can lead the problems too
because now we're actuallyforcing the chisel out of a straight position which really isn't goodfor the long run either. the bottom line is for me personally, the no deflection methodis the best way to go and the way that i fight the heat build up is to just have really,really sharp tools. that's the next thingwe're going to focus on let's sharpen up amortising bit and chisel.
i'm going to start bytouching up the ogre bit. generally speaking idon't do this very often and frankly the lessmaterial you'll remove from a bit the better. i really just do it to doa little bit of touch up here and there. let me show you the process. if you want, you can usea specific file for this, they actually do have ogre bit files
and you probably havesome files in the drawer that would work but i really prefer togo a little bit lighter and i use these littlehoning, diamond honing plates and they're on a nicelittle plastic stick. it's very easy to get in here. you could sharpen router bits this way and for something like thisi find this to be perfect and it's not very aggressive which is good
because i just don't want toremove a whole lot of material. i'm going to go with the super fine and we'll do a little touch up work. i'm really only going tofocus on my cutting surfaces and you want to be careful not to change the dimensions of the bit. we have to keep that in mind as we go. here's one area that canuse a little touching up, that's this bevel right there.
i'm just going to take the honing plate. i don't really want tochange that bevel angle. i just want to clean it up a little bit. if you want, you could certainly put a little bit of water on there. help things go a little smoother. that's looking pretty good. now if you feel a significantburr developing here, you may want to justtake a quick pass or two
but you really don't want to work that underside too much. just focus on the bevelof the cutting edge here. now you have another spur that runs around and helps keep the hole nice and circular. sort of severs materialin the outside edge as this piece is justkind of peeling it away. we do want to make surethat this inside surface gets a little activity here.
now this shape shouldbe a little bit concave so it's really not the end of the world if you do short strokesjust to make sure that you sort of maintain that concave shape. you don't necessarilywant to flatten it out which eventually you could very well do if you keep doing long strokes across both of the high points. now the final thing we want to address
is the center spur. you basically have three phases and they're all nice and flat so it's fairly easy to clean those up. a little bit of touch up like that. now, one thing you want to avoid doing is working the outside edge. think about it, if youstart removing material from the outside here,what are you going to do?
you're going to changethe effective diameter of this cutting surface. only inside edges and cutting edges and you should be fine. now for the chisels, youwant to treat the surface like you would the back of any chisel. we want to make sure thatit's nice and flat and clean and if you remove all ofthose machine milling marks, you'll find that the chiselis much easier to pull out
of the work after you plunge it in. depending on the sort of levelof scratches you have here for the manufacture sort of determines what grit you need to start with but most times i find idon't need to go any lower than a 1,000 grit. that's what i have here,just a 1,000 grit waterstone. in fact this is a shapton ceramic stone and i'm going to give acouple passes on each phase.
i only really work the bottom because at least the chiselsthat i have access to, most of them dip in just slightly so the business end. this bottom half inch is really the thing you're most concernedabout being nice and flat. if you work it too much, you could very well change the orientation so it's out of square.
it would be bad news. just put pressure downwith my index finger. move it forward and back and in no time, you should start to see ittaking up a nice shine as you go. i'll polish that upjust a little bit more. now you could see most of the factory, no marks are gone. i just have this little tiny bit here but if you look down at the tip,
it's pretty much clean from point to point all the way around that surface and that's really themost important thing. i'm really not too concerned about this and you could work it a littlebit more if you want to. i just don't feel the need to do that and i think this helpsto maintain the integrity of the original size of this chisel. if i push it too much,
i can actually change itsdimension which is no good. i'm going to do the same treatment on the other three phases. once all four phases are done, i'm going to move to my 5,000 grit stone and i really am treating this pretty much like a regular chisel. just polish up each phase. now the outside phases of ourchisel are nice and polished
up to 5,000 grit but as we know with chisels,that's only half the battle because we have a bevel that needs to be sharpened on the inside. unlike a regular flat chisel, this bevel is a littlebit more complicated. how the heck are we going to sharpen that? unfortunately there aresome things out there that are made solely for this purpose.
let me get the chiselmounted into the device. try to get it as closeto vertical as you can and here is one such kit. basically it comes with a handle and two cone shaped diamond sharpeners and these are meant tofit down inside the chisel and you just kind of spin them around and it sharpens it up. we've got what they call one,
that's basically coarseand the other is fine. use the fine if you have to, if you don't see much progress you might want to switch to the coarse but i always like to use the fine first because i don't want toremove anymore material than is necessary. once you have the one you want, pop it into the little handle here.
your goal is to spin the cone, sharpen the interior bevel while trying to keep everything as perfectly vertical as possible and that's really the challengewith this particular setup. let me show you the second option because i think that oneis a little bit better. this one works in a very similar way. you could see i have thissort of conical shaped
sharpening element here but the difference is ihave these little pilots that will go into the hole on the front and that actually willhelp not only guide this but help me stay perfectly vertical. i've got a three-eighth inch chisel here. i'm going to pop in a three-eighths pilot and tighten a little set screw. it does recommend in the instructions
that you do this by handand do not use a drill so i'm just going to use the little handle from the other kit. now i just drop the pilot in place and that actually isgoing to go a long way in helping me keep thisperfectly vertical. how do you know you're finished? it's actually pretty easy. just use your fingers to feel the edges
and if you feel a little metal burr there, that means that the metalhas been honed enough that it's actually foldingover the edge a little bit. i definitely have a burr on all four sides so let's head back to the 5,000 grit stone and we'll remove that burr. now removing the burr takesalmost no effort at all. just about three strokesper side should be enough and if you feel it with your fingers,
there shouldn't be anything there anymore. now the good news is that process that i just showed you iswhat you do with a chisel that's straight from the factory. it needs a little bit more work than one that we've already honed. in the future when thischisel becomes dull, i'll take it back to the bench. i will start by honingthe bevel on the inside
that's going to create thatburr along the outside edge so i'm just going to take it from there to my 5,000 grit stone. polish up the outside edgesand the chisel is done. it's much easier once youdo this the first time with the factory chisel. now as a final preventative measure, i like to use a siliconefree dry lubricant on both the bit and the chisel.
it basically goes on wet and then dries a couple seconds later. i'm going to wipe off the excess and that will keep thisbit nice and lubricated and a lot less likely to sortof gunk up with woodchips. now to maintain the mortiser itself, i recommend using some form of lubricant on any moving part. that means the dovetail ways,
if you have any gears or things like that, you just want to keep them well lubricated and you kind of have two choices. i usually recommend eitherwhite lithium grease or a dry lubricant. here's the thing, the white lithium grease is probably going to lubricate better. the drawback is it tends tocatch more dust and debris
whereas the dry lubricant, maybe it doesn't lubricate as well but you're less likely to accumulate dust and that gook that sortof gets around anything that's oil based andlubricated in the shop. for me, i like the drystuff a little bit better and i like to spray alittle bit on any spot where there's metal to metal contact and that should help itmove nice and smooth.
that in a nutshell is thehollow-chisel mortiser. it is a heck of a tool. now depending on your budget, depending on the amount ofspace you have in your shop. you may or may not think that this is a worthwhile purchase because it really only does one task and think about it, thereare other tools out there that we use to cut mortises that also do
a ton of other thingsfor instance the router. a lot of times a routeris a more sensible choice when you're first startingout and stocking up your shop but if you get to the pointthat you need to batch out a bunch of mortises quickly, you want to do it in a waythat's very easy and repeatable. you just can't beat ahollow-chisel mortiser. it's definitely a good optionthat you should check out. thanks for watching andwe'll catch you next time.
(mellow music)